Why people will remain at the heart of the factories of the future
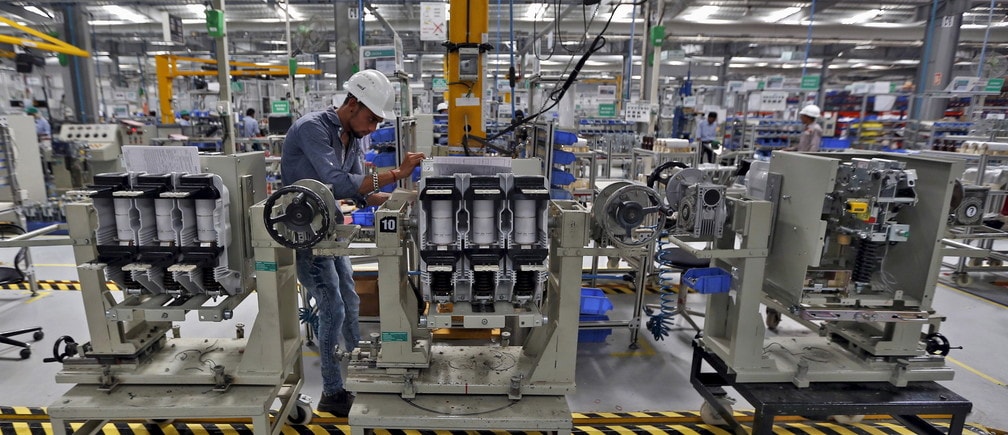
Digitalization won't replace humans in factories - its successful implementation depends on them Image: REUTERS/Amit Dave - GF20000058870
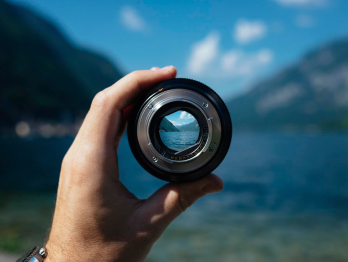
Get involved with our crowdsourced digital platform to deliver impact at scale
Stay up to date:
Future of Work
There is no denying that we are well into the swing of the Fourth Industrial Revolution. Early adopters of digitalization are already seeing measurable benefits, such as increased energy efficiency and quicker troubleshooting - which means less downtime of their assets and a better return on capital expenditure. However, there is still concern that digitalization will not be accepted or adopted by the workforce, or that knowledge will be lost.
How can we manage this and make sure that the benefits of digitization can be adopted at scale and diffused throughout the industrial ecosystem?
Our answer: empower your people.
Equipping operators with mobile devices, data analytics, augmented reality and transparent connectivity means decision making will be smarter and faster - and manufacturers will be able to deliver on increasingly strident market demands for more flexible and sustainable manufacturing. For example, collecting and analysing data can enable new and different behaviours and operating procedures – such as using process data to extend the life of connected industrial assets, or simulation and scenario-planning tools that can suggest more sustainable solutions in areas like raw material selection, choosing the most optimal energy supplier, or recommending the most suitable delivery method.
In smart factories you will not only see intelligent new technologies that can even be self-learning, but you will see these new technologies working seamlessly with highly skilled operators to increase productivity and operate the plant in real time. The human element in gathering, comparing and analysing data is essential.
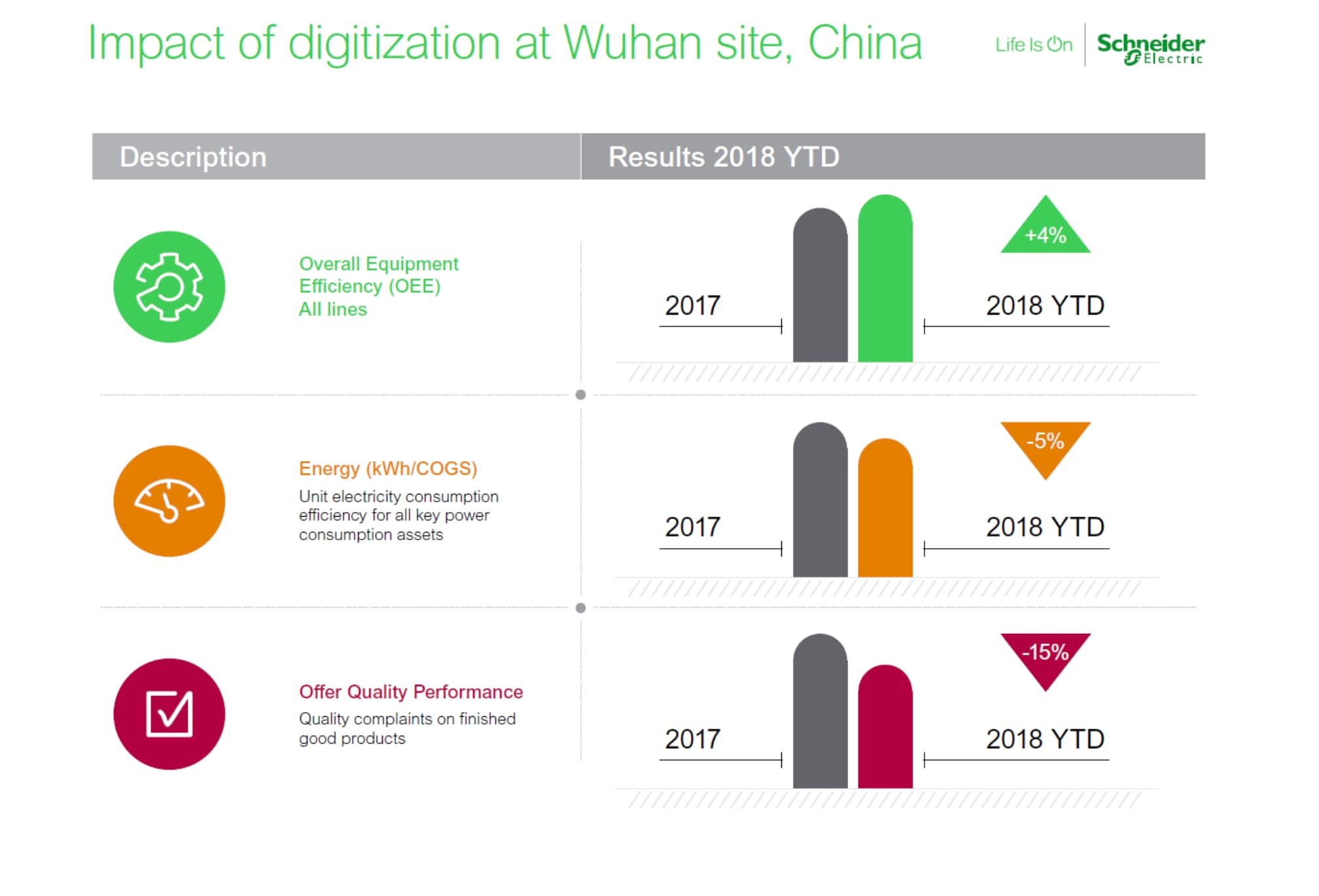
Connectivity between products, machines and people, and collaboration between people across the complete industrial value chain, are the enabling factors of digitalization. If there is a risk to the success of the widespread adoption of digitalization it is how companies manage the journey - how they train their people to step up and embrace the changes that smart manufacturing brings to their day-to-day work.
A culture that drives and manages innovation and the proper implementation of new technologies is important - but it’s not enough. People need to experience the benefits first-hand. We have found through our own digitalization journey that pilot phases, peer-to-peer learning and cross-site collaboration have been most effective in ensuring the rapid adoption and appreciation of new technologies by our workforce. Our people were looking for ease-of-use and learning opportunities, and have benefited greatly from a better ability to transfer knowledge among themselves on what fixes or adjustments have been made to processes, and so have been able to be more predictive of downtime risks.
In a relatively new factory in China, with high revenue growth and limited resources, we have seen compelling results that drive the case for digitalization:
- A 15% decrease in quality issues
- A 5% decrease in energy consumption
- A 4% increase in overall equipment efficiency
But it’s how we’ve gone about achieving those results that point to the people power in this plant.
Our Wuhan site has become a showcase factory in Asia where experts in machines, plants and power have taken on an ambassadorial role in order to drive the changes required to reap the benefits of digitalization. They have built a standard architecture that encompasses all their best practices and have begun to roll it out across China. This has facilitated cross-site collaboration on the implementation, testing and scaling up of new technologies like digital energy Management systems, advanced production scheduling, and automation using collaborative robots and automatic guided vehicles.
These ambassadors have a significant role to play in internal training. They have trained more than 300 people and have taken on the role of recreating, testing and fixing real customer problems from across the region.
In addition, best practices are not only shared on operational changes, but across other departments like finance and human resources to ensure the entire ecosystem is prepared for the factory of the future.
We may think that smart manufacturing is all about connectivity – but it’s collaboration that is going to take industrial companies to places they never dreamed possible.
Learn more about the World Economic Forum’s system initiative on Shaping the Future of Advanced Manufacturing and Production
Don't miss any update on this topic
Create a free account and access your personalized content collection with our latest publications and analyses.
License and Republishing
World Economic Forum articles may be republished in accordance with the Creative Commons Attribution-NonCommercial-NoDerivatives 4.0 International Public License, and in accordance with our Terms of Use.
The views expressed in this article are those of the author alone and not the World Economic Forum.
Related topics:
The Agenda Weekly
A weekly update of the most important issues driving the global agenda
You can unsubscribe at any time using the link in our emails. For more details, review our privacy policy.
More on Jobs and the Future of WorkSee all
Roman Vakulchuk
April 24, 2024
Eli Joseph
April 19, 2024
Kate Whiting
April 17, 2024
Juliana Guaqueta Ospina
April 11, 2024
Victoria Masterson
April 9, 2024