Green steel for Europe – a path of small steps and giant leaps
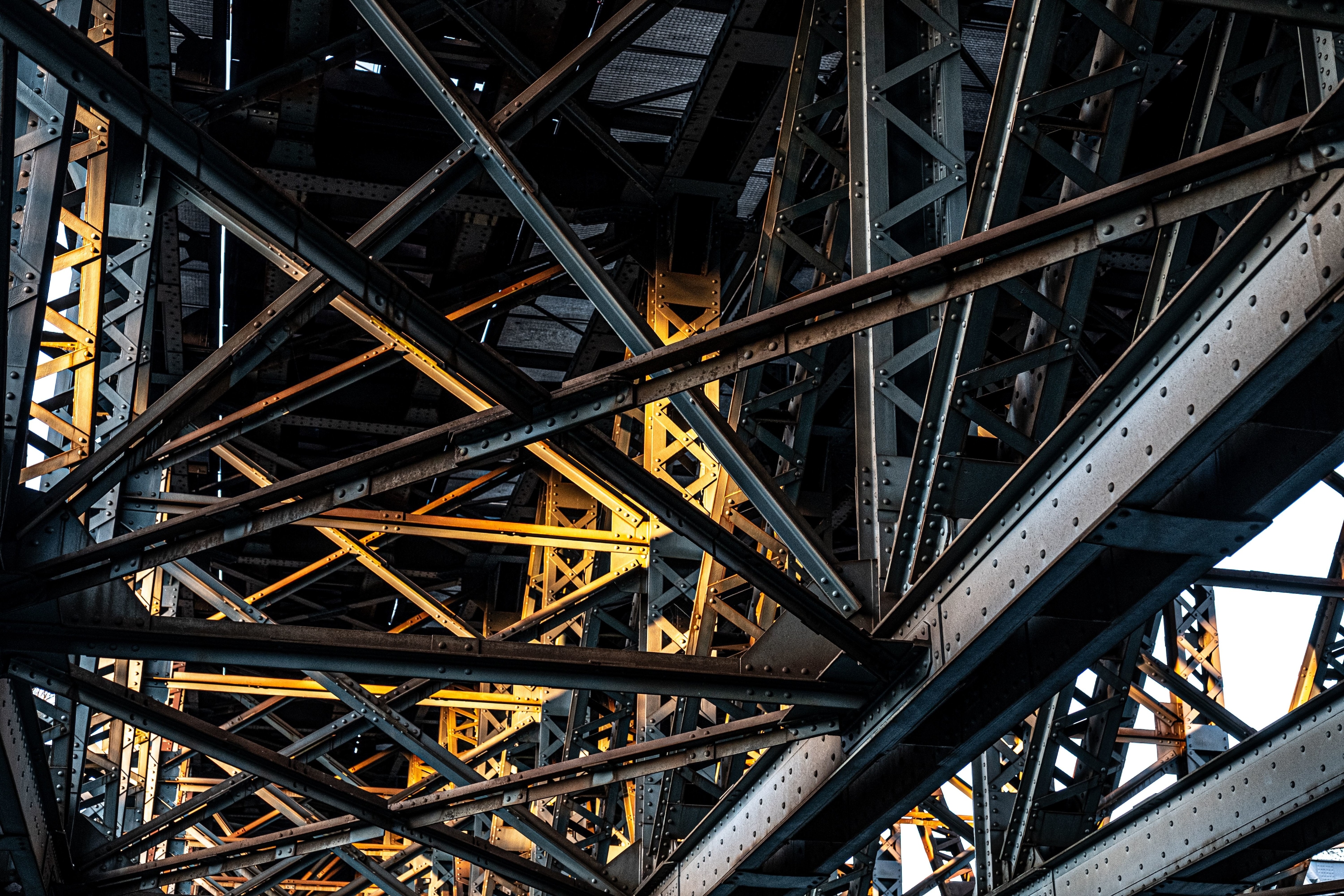
Time to turbocharge the green steel industry. Image: Unsplash/Luca Upper
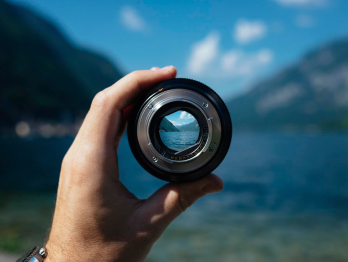
Get involved with our crowdsourced digital platform to deliver impact at scale
Stay up to date:
Davos Agenda
Listen to the article
- Steel is a key ingredient in our modern world and, used in everything from buildings to bicycles, it is very CO2 intensive.
- The biggest leap in greening the steel industry comes from energy sources and production methods, with a future looking towards carbon-light technologies.
- The carbon footprint of European steel production can be meaningfully reduced through localisation of feedstock.
Steel – a key ingredient in our modern world, used in everything from buildings to bicycles – is very CO2 intensive. Its production is responsible for around 5% of CO2 emissions in the EU and around 7% globally.
We cannot live without it. So how can we live with it? We need to take leaps – big, expensive and complicated leaps – with huge payoffs for green steel. And we need to take smaller, easier and faster steps to greener steel.
Big changes, such as the move from gas to electric lighting, can take decades to implement and involve massive new infrastructure. But incremental improvements can also have a big impact while being simple and inexpensive to put in place. An example is optimising combustion efficiency: when you mix just the right amount of oxygen with natural gas, you get the hot, clean-burning blue flame of a modern stove, instead of the sooty yellow flame of an unregulated burner.
With enough steps, we can climb a mountain. We just need to make sure the steps are in the right direction.
Europe's Green Deal sparks action
Europe’s Green Deal is prompting industries to examine their processes and supply chains to better understand where their CO2 emissions happen and how to shrink the overall footprint. Technology is a key driver in this exercise, helping businesses collect the data they need, not just from their own operations, but also from those of their entire supply chain. Businesses need data to know their steps take them in the right direction.
For the steel industry, the biggest leap in greening comes from energy sources and production methods, with a future looking towards carbon-light technologies, such as hydrogen-powered direct reduced iron production (DRI), as opposed to coal-fired blast furnaces (BF).
Around 60% of Europe’s steel production is based on BF iron production from iron ore, with a tonne of steel resulting in around 1.9 tonnes of CO2 emissions. The remaining 40% of Europe’s steel production, comes from natural gas-fired DRI, some using recycled scrap material as feedstock, resulting in a more modest 1.4 - 0.4 tonnes of CO2 per ton of steel. Importantly, this more circular process using recycled material is greener, but the resulting metal is considered inferior and is only suitable for certain applications.
Green hydrogen can help green steel
Making the biggest leap to green steel requires substituting natural gas in a DRI plant with hydrogen. But not just any hydrogen – it must be 'green' hydrogen. Today, the vast majority of hydrogen is produced in a process that uses natural gas. This is known as 'grey' hydrogen. To truly green a DRI plant, it must be fed with green hydrogen, produced through electrolysis using water and electricity from renewable sources, such as wind and solar.
Europe’s next-generation steel production is focused on precisely this. Using green hydrogen and DRI production circuits, the goal is to close the gap of circa 1.3 tons of CO2 per ton of steel that arises from BF use. This huge shift is expected to require over €180 billion of investment in steel plants, hydrogen electrolysers and additional renewable energy sources.
€180 billion is a lot of investment. Mobilising such a mountain of capital – especially in a high-rate environment – requires a complex web of government support, regulatory threat and commercial boldness. The work for this is underway, but it takes years.
In the meantime, what steps can we take?
This was a question recently asked by Aethel Mining, which operates Europe’s second-largest iron deposit. Aethel Mining uses software from Dorae – a World Economic Forum Global Innovator and previous Technology Pioneer – to manage much of its day-to-day operations and its product planning efforts. Aethel Mining used the information it captured with Dorae – everything from machine hours to lab results and logistics movements – to calculate the carbon footprint of its own operations and those of its potential distribution pathways, as compared to other supply chains for steel.
The result? The insight that the carbon footprint of European steel production can be meaningfully reduced through localisation of feedstock.
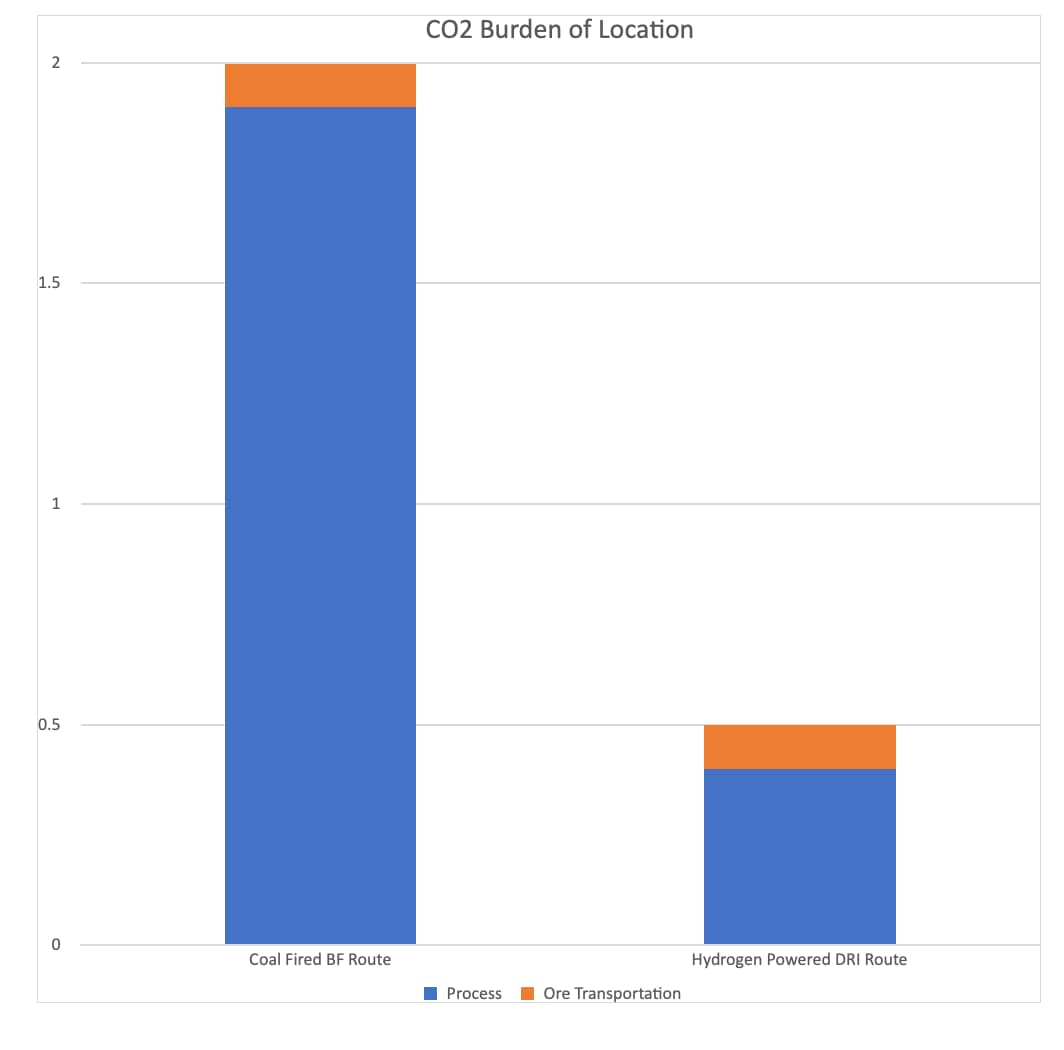
Much of the world’s steel is produced in China. In addition to the energy required to transform iron ore into iron and in turn into steel, the ore must reach the place of processing. An efficiently paced round trip Capesize vessel voyage carrying iron ore from Brazil to China takes about 90 days and burns almost 3,500 mt of fuel oil. This equates to circa 10.5 thousand tons of CO2 for the voyage and 0.11 tons of CO2 per ton of metal produced from the ore.
Reducing this emissions burden may not be a huge leap, but it is a meaningful step. By supplying iron ore from within the heart of Europe, Aethel Mining can deliver CO2 savings to European steel production. 0.11 tons is a fraction of the CO2 emissions targeted by new energy and industrial infrastructure – but it can be done now, not in years and it doesn’t cost €180 billion. In fact, it saves money on transportation and proximity makes for a more reliable supply chain.
As Faraday and Bunsen did in the 1800s, we can gather and connect the information to make incremental improvements in things as basic as fire or the choice of a supplier. Technology can help us cast the informational net wider and deeper and move faster, so we can take smaller immediate steps for sustainability while we work over decades on the bigger leaps.
Don't miss any update on this topic
Create a free account and access your personalized content collection with our latest publications and analyses.
License and Republishing
World Economic Forum articles may be republished in accordance with the Creative Commons Attribution-NonCommercial-NoDerivatives 4.0 International Public License, and in accordance with our Terms of Use.
The views expressed in this article are those of the author alone and not the World Economic Forum.
Related topics:
The Agenda Weekly
A weekly update of the most important issues driving the global agenda
You can unsubscribe at any time using the link in our emails. For more details, review our privacy policy.
More on Forum InstitutionalSee all
Gayle Markovitz
April 28, 2024
Gayle Markovitz
April 27, 2024
Mirek Dušek and Maroun Kairouz
April 27, 2024
Kate Whiting
April 26, 2024
Spencer Feingold and Gayle Markovitz
April 19, 2024
Kate Whiting
April 17, 2024