From remanufacturing to recycling: how manufacturing can raise the bar on global climate goals
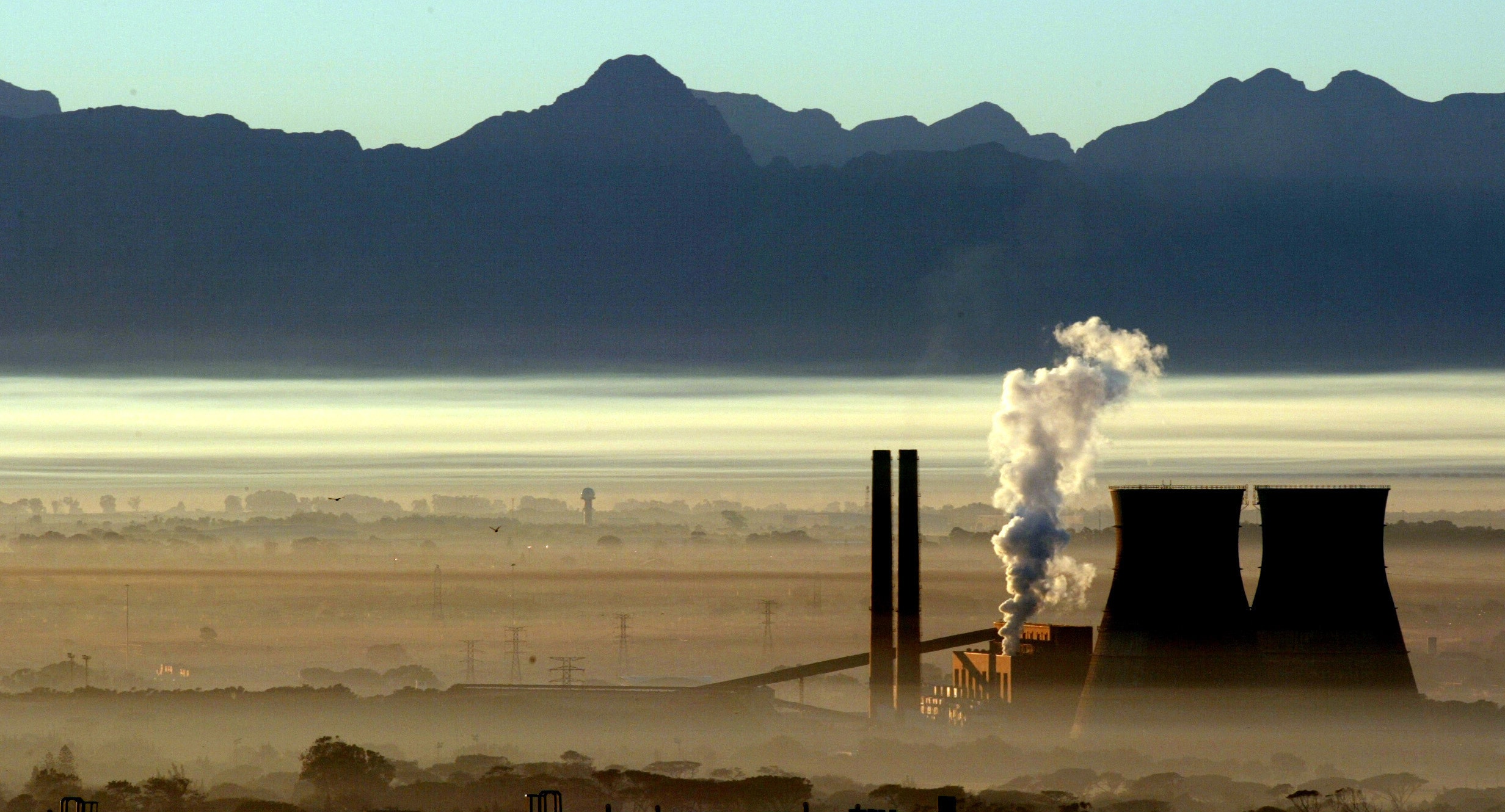
In the US, manufacturing accounts for almost a quarter (23%) of direct carbon emissions Image: REUTERS/Mike Hutchings
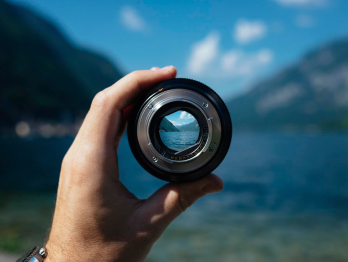
Get involved with our crowdsourced digital platform to deliver impact at scale
Stay up to date:
Automotive and New Mobility
Listen to the article
- Improving resource efficiency in manufacturing processes is as important as reducing the transport industry’s greenhouse gas emissions;
- Setting high emission reduction targets is the only way towards a net-zero greenhouse gas economy;
- Reducing the industry's reliance on fossil fuels, recycling components and adopting more environmental design practices will be critical, as will insisting on a better way of working across the value chain.
The manufacturing industry must accept its heavy responsibility for emissions of greenhouse gases. In the US, manufacturing accounts for almost a quarter (23%) of direct carbon emissions, according to the Environmental Protection Agency. In Europe the situation is equally dire: the industry emits an annual total of 880 million tonnes of carbon dioxide equivalents making it one of the largest emitters of greenhouse gases on the continent.
Sweeping changes need to be made – and thankfully are being introduced – across every aspect of manufacturing if we are to collectively transform our operations and products and future-proof business growth. More than a thousand companies have committed to the Science Based Targets initiative, which calls for real action to limit global warming. As part of this, a few hundred organizations, including Volvo Group, have committed to the Business Ambition for 1.5˚C goal which targets a net-zero greenhouse gas value chain by 2050.
At Volvo Group, we are committing to do this a decade earlier, by 2040, and have developed our own more ambitious plan to reduce transport emissions for trucks and buses to meet the 1.5˚C goal. But talking is not enough – we need action.
As a major vehicle manufacturer, the biggest challenge for us is still connected to emissions during the use of our products. This accounts for the highest proportion of our complete CO2 footprint, which is why we focus on electromobility and other fossil-free solutions to mitigate the impact. Yet, while it may be a smaller percentage, we simply cannot forget the remaining emissions resulting from the manufacturing and transport of those same products.
From ‘take-make-waste’ to ‘reuse, reduce, recycle’
Overproduction, waste and an overreliance on fossil fuels have historically been significant contributors to emissions in the industry, but manufacturers are now taking major strides to reverse this trend. One philosophy has been critical to this change: the circular economy. It focuses on optimization across the value chain, finding efficiencies in production processes and adopting a “reuse, reduce, recycle” approach to make manufacturing more sustainable. The circular economy must be part of the initial product development and design process.
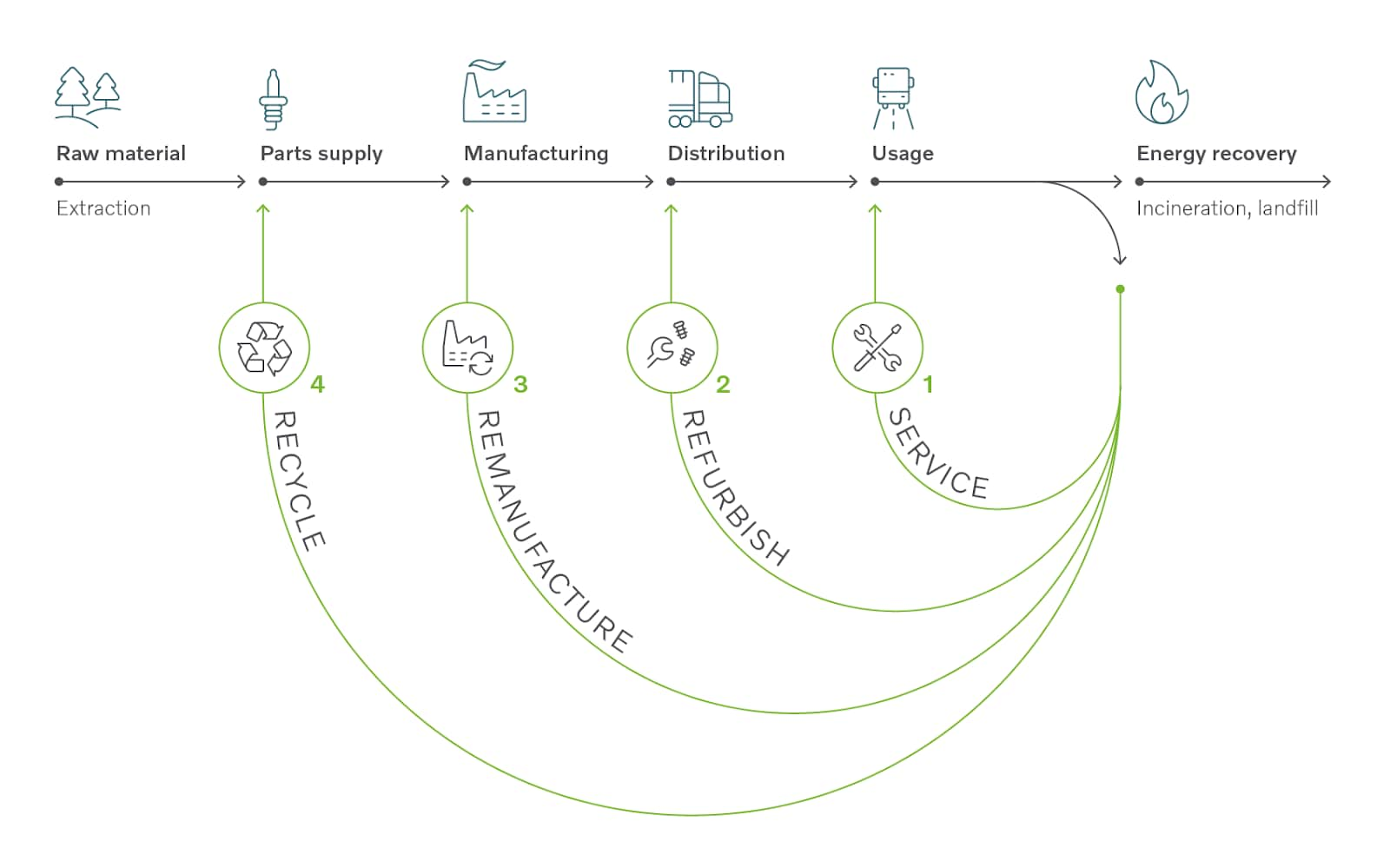
It's working. BatteryLoop, an initiative delivered by Stena Recycling, has devised a smart energy storage system that promotes circular energy use with its batteries. For example, batteries used to power a bus can also be used to provide power to a residential complex. Another demonstration of the circular economy in action is the defined goals within the Paris Agreement. Putting this philosophy at the heart of global climate change targets is a clear indication to the wider industry and society in general of how important the circular economy will be to collectively reduce our carbon impact.
Remanufacturing – the challenging process of making used parts come to life again through recovery, disassembly and repair – and the recycling of components are two vital ways to make manufacturing more sustainable. At Volvo Group, we harvest used parts and components from vehicles for incorporation into new vehicles and even remanufacture diesel particulate filters. The energy required to remanufacture our parts is, for some parts, up to 80% less than to manufacture a product from scratch. We have also set up a dedicated business area, Volvo Energy, to strengthen batteries' performance and offering over their entire life cycle and look at ways to give batteries a second life in different applications.
The recycling of materials is important to increase resource efficiency. The Environmental Protection Agency estimates that secondary steel production uses about 74% less energy than the production of steel from iron ore (sometimes referred to as virgin steel). Obviously, we need to use as much secondary steel as possible but, in order to continue supporting economic growth around the world, we will still require a lot of virgin steel in the future, as long as it is produced sustainably. In fact, it will soon be possible to create 100% fossil-free steel using fossil-free electricity and green hydrogen, resulting in a much lower climate impact. The need for steel will grow significantly in the long term and newly made fossil-free steel will be needed to meet this demand.
Wider adoption of new technologies, processes driven by artificial intelligence (AI) and techniques such as additive manufacturing (using 3D printing technology to produce tools and parts to enable quicker production and continuous quality improvements) can also go a long way to reducing the environmental impact of our manufacturing, processes and services.
The world is changing and the potential is there for all manufacturers to use this digital transformation to do things better. We can no longer only look inward but must look beyond our own operations towards all other parties along the supply chain.
A more sustainable way of working
Manufacturing operations only tell a part of the story. We know that the business of manufacturing is a partnership, so emission responsibility calls for investment in our future from everyone along the supply, distribution and logistics chain.
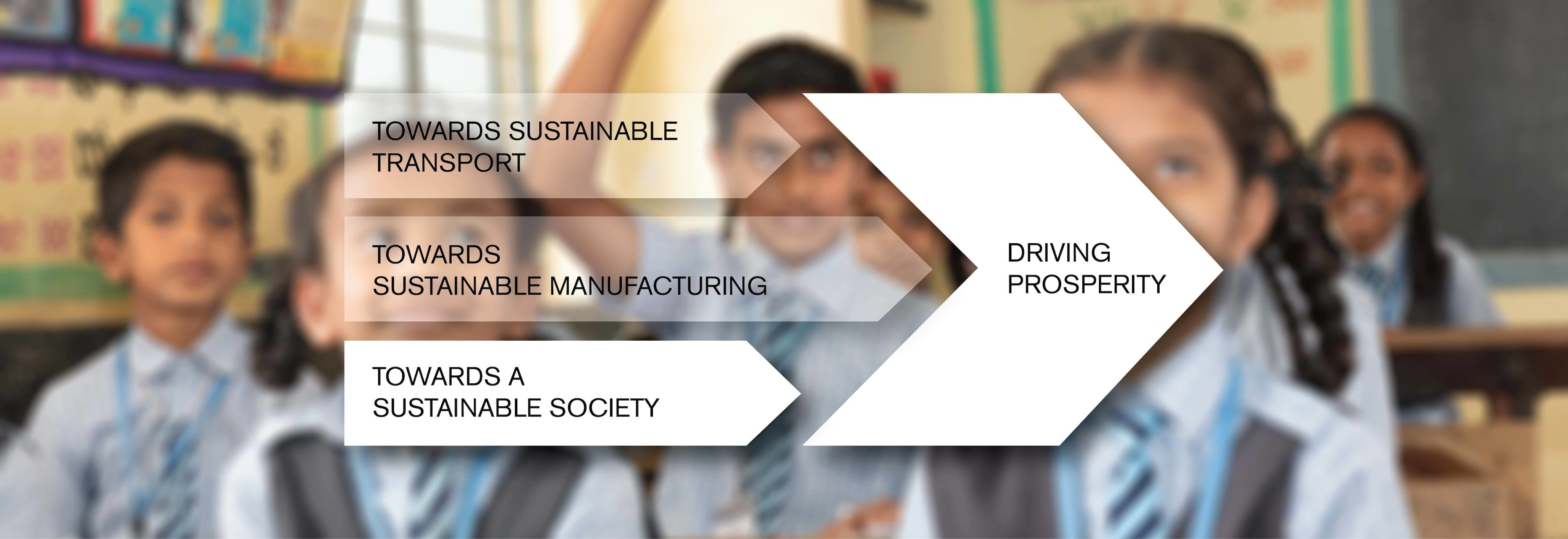
Insisting on responsible behaviour and responsible purchasing decisions across every area of production and placing high demands on all players is the only way to ensure continued environmental improvement. The onus is on everybody, including major global manufacturers, local suppliers, governments and policy-makers, to make sure components, parts, services and systems are delivered in a way that supports a more environmental way of working. Only by working together can we hope to deliver more sustainable manufacturing.
Don't miss any update on this topic
Create a free account and access your personalized content collection with our latest publications and analyses.
License and Republishing
World Economic Forum articles may be republished in accordance with the Creative Commons Attribution-NonCommercial-NoDerivatives 4.0 International Public License, and in accordance with our Terms of Use.
The views expressed in this article are those of the author alone and not the World Economic Forum.
Related topics:
The Agenda Weekly
A weekly update of the most important issues driving the global agenda
You can unsubscribe at any time using the link in our emails. For more details, review our privacy policy.
More on Climate ActionSee all
Ewan Gribbin and Deepanshu Singh
July 26, 2024
Gabi Thesing, Ian Shine and David Elliott
July 25, 2024
Luis Alvarado
July 24, 2024
Kate Whiting
July 23, 2024
Natalie Marchant and Julie Masiga
July 19, 2024