How circularity can increase profits in cement and concrete
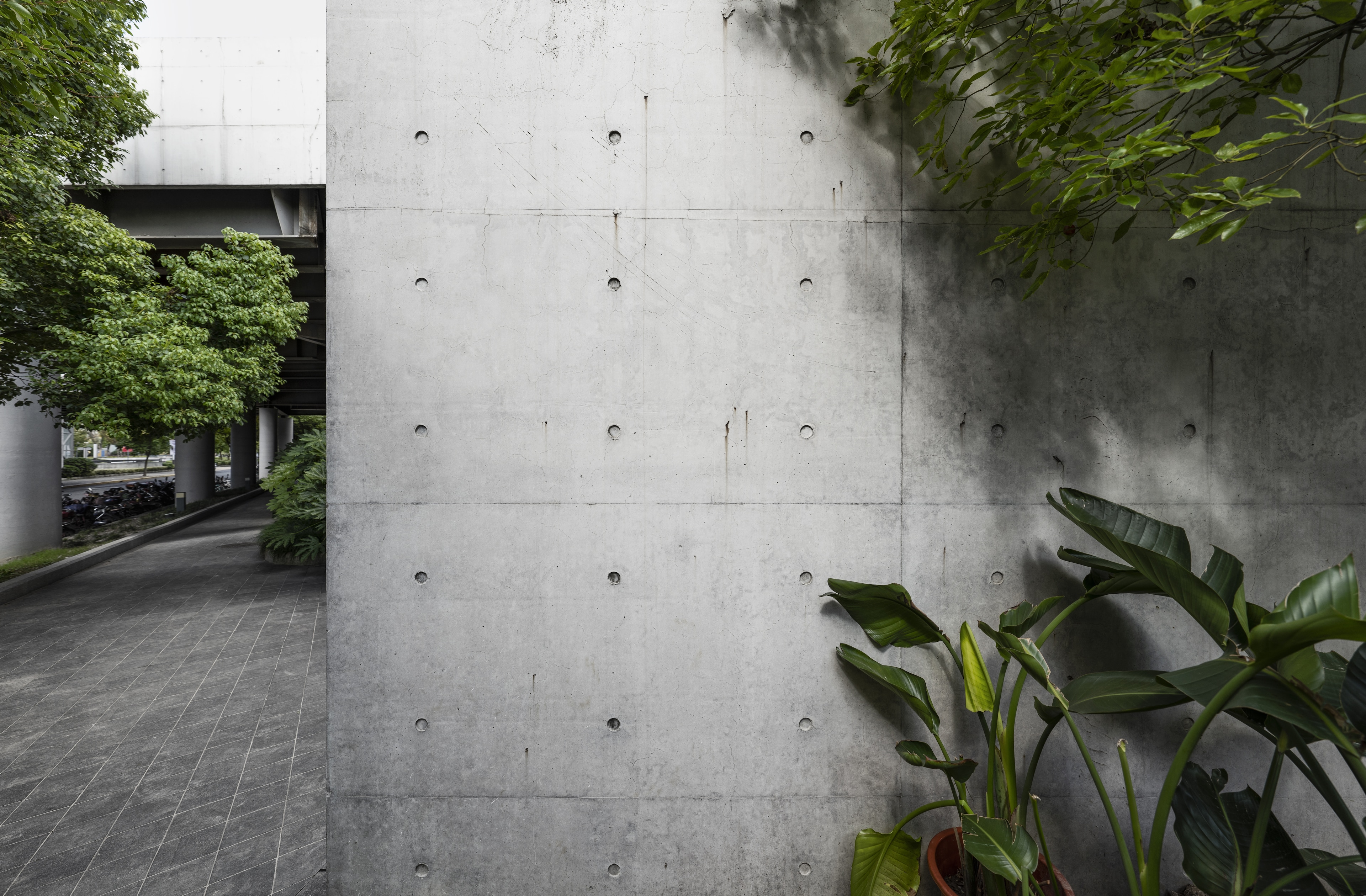
Circularity technologies are still not widely utilized in the built environment. Image: Getty Images
Jorgen Sandstrom
Head of Energy, Materials, Infrastructure Programme, Industrial Transformation, World Economic ForumYvonne Leung
Global Strategic Engagement Lead, Philanthropy for Nature and Climate, World Economic ForumSebastian Reiter
Partner, McKinsey & Company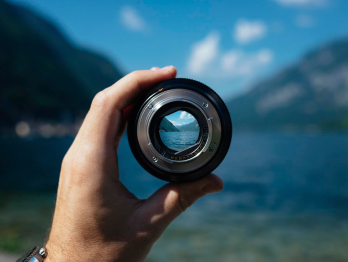
Get involved with our crowdsourced digital platform to deliver impact at scale
Stay up to date:
Engineering and Construction
Listen to the article
- Facing rising carbon and landfill costs, the concrete and cement industries can embrace the circular economy as an opportunity to unlock value.
- The industry can create circular loops in the areas of CO2 recirculation, materials and minerals, and energy.
- Roughly 2.6 billion tonnes of CO2 emissions could be avoided or mitigated through applying these technologies by 2050.
Concrete and cement, which account for approximately 7% of global CO2 emissions, are facing several trends with potentially far-reaching cost implications.
General carbon prices have almost reached €100 per tonne of CO2 in the European Union, a level that could become the norm by 2030. European regulations such as Fit for 55 add further financial pressure and incentives. At the same time, landfill costs from construction and demolition waste (CDW) affect the entire building ecosystem, with prices reaching €150 a tonne. Bearing in mind global average prices for CO2 and landfill, these costs could total approximately €210 billion in 2050. In addition, rising energy prices are increasing production expenses for traditional materials such as cement and concrete.
To date, circularity technologies and circular business models have been viewed as an opportunity for decarbonizing the built environment, a perspective that significantly underestimates their impact. Joint research by the World Economic Forum and McKinsey estimated these technologies can decarbonize up to 80% of cement and concrete emissions (based on a cement demand of 4 billion tonnes in 2050), while reining in costs. Here is how companies can achieve a positive financial impact from circularity in cement and concrete.
Cement and concrete production – and by extension the building and construction value chain – offers many opportunities to create circular loops. Circularity technologies are mostly nascent and fall into three clusters: CO2, materials and minerals, and energy; the recirculation of materials and minerals being the most prominent cluster. According to our estimates, all of these circularity technologies could be profitable at expected carbon prices. They also have the potential to contribute significantly to CO2 abatement across the built environment (see below).
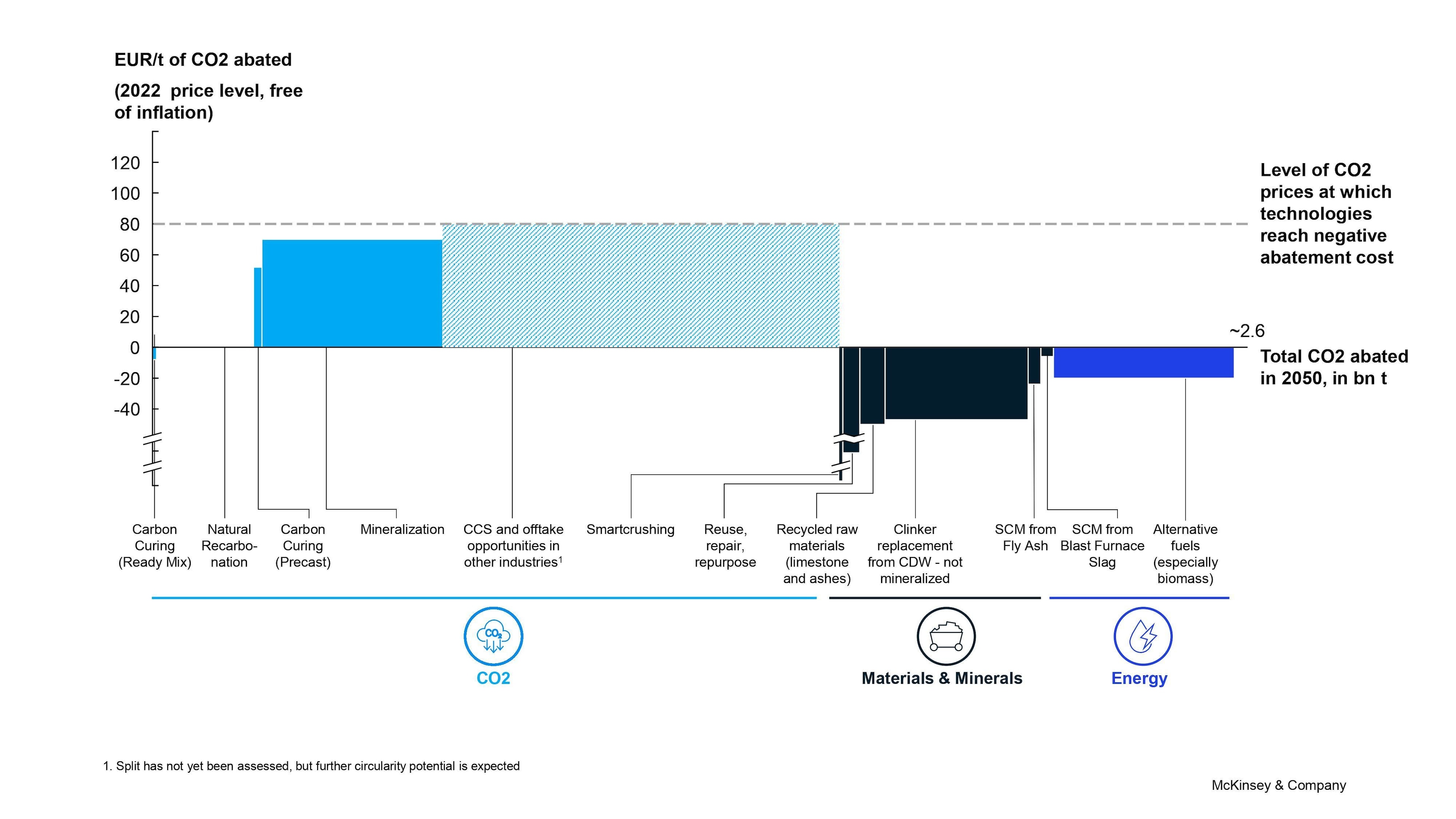
1. Recirculation of CO2
CO2 emissions from cement and concrete processes can be reinserted into the value chain. Key technologies in this field include the curing of ready-mix or precast concrete; the enhanced recarbonation of CDW (carbon sink in different types of waste products); the mineralization of aggregates from concrete waste or other waste material; and carbon capture and storage (CCS) or other use cases of CO2 such as in the chemical industry. While most are not yet deployed at scale, they could eliminate up to 1.5 billion tonnes of CO2 by 2050, according to the assumptions of this new research.
These technologies could generate further financial value. Carbon curing in ready-mix concrete already offers negative CO2 abatement cost through the reintroduction of carbon. While the estimated CO2 abatement potential of this technology is relatively low, it could add further value in countries with high CO2 pricing mechanisms.
CO2-offtake technologies will likely be implemented first in regions with rapid growth in carbon pricing mechanisms, such as Europe or North America. In the United States, for example, the Inflation Reduction Act of 2022 includes roughly $370 million for investments in climate mitigation and green energy over the next decade.
The increased CO2 abatement cost is mainly caused by the novelty of some technologies and the high cost of capturing pure carbon for most. However, only some of the analyzed technologies, such as carbon curing or storage, require pure industrial captured carbon. Others that use direct exposure to flue gas from a CO2-emitting production site can achieve lower costs. For example, enhanced recarbonation and mineralization of aggregates from mineral waste is estimated to start at €50 per tonne of CO2 at current price levels (free of inflation). Such CO2-offtake technologies are expected to be cheaper compared with CCS.
Cement and concrete manufacturers could explore solutions based on the development of carbon pricing in their respective region. A potential next step is exploring CO2-offtake opportunities in other industries (including plastics and chemicals), highlighting the need for increased collaboration across industries.
2. Recirculation of materials and minerals
This category includes the recirculation of industrial, municipal and agricultural waste materials: for example, by directly reusing entire structures or recycling waste into gravel for road construction, aggregates for concrete, as replacement for clinker, or using decarbonated limestone as a raw material. Two pathways exist: First, cement and concrete manufacturing can use waste material from other industries. This includes – alternative fuels set aside – mainly metal slags or fly ash, which can be used mainly to replace clinker. Second, waste materials from the industry and demolished buildings could be recirculated back into cement and concrete production or or other industrial processes, such as for basements in road construction.
Similar to the recirculation of CO2, direct use of materials and minerals has a significant impact on total CO2 abatement. Factors include the reduced amount of cement needed (such as through unhydrated cement fines in crushed concrete aggregates) and clinker (using CDW as a filler to decrease the clinker factor), as well as the use of decarbonated raw materials to replace limestone in clinker production.
In addition, as most recycling technologies are expected to have negative CO2 abatement costs in countries with waste or landfill costs, the lower costs of these technologies allow for quick wins in CO2 abatement. Mechanical recycling processes operate relatively cheaply compared to chemical treatments and landfill. Aggregates from CDW can be the same cost as virgin sand and aggregates for concrete, depending on the transportation expense from the demolition site. Since the availability of mineral waste is a limiting factor, utilization of CDW will likely shift from traditional recycling methods to more innovative solutions with higher CO2 impact: for instance, from gravel for road construction to fine crushing of concrete aggregates or extraction of decarbonized limestone.
3. Recirculation of energy
This category comprises the use of alternative fuels from waste material and the recovery of energy and heat throughout cement and concrete production, providing a growth avenue for cement players facing an overall flat demand in their core business.
Given the low cost of waste material and increasing prices of traditional energy sources such as petcoke, alternative fuels often come at a negative cost of approximately €20 per tonne of CO2 at current price levels compared with the business-as-usual scenario (global average, varying depending on geographies and types of waste material). Biomass, with its net-zero emissions, is expected to offer a much greater impact on CO2 abatement.
The 2050 Cement and Concrete Industry Roadmap for Net Zero Concrete, published by the Global Cement and Concrete Association (GCCA), forecasts the global share of alternative fuels in the industry could reach 43% by 2050. These estimates are rather conservative, as alternative fuel is a mature technology that can already be used. The greatest value potential arises in countries and regions with a high availability of waste material and high landfill costs. Cement and concrete production can provide an offtake opportunity for waste material, which could be supplied for free or even at a negative cost by the producing industries. The recirculation of energy is an area where the industry has made impressive strides to capitalize on opportunities. Alternative energy is an area where cement and concrete manufacturing can be part of the waste management solution.
Opportunity for circularity in the built environment
External factors, especially CO2 prices, decarbonization subsidies and costs of landfill, can potentially further unlock the value of circularity technologies. Cement and concrete producers (and other ecosystem players) should double down on circularity. To win, they need to evaluate and select circular technologies based on these questions:
- Can a cost-benefit position be achieved with existing CO2 prices, landfill costs, and regulatory frameworks?
- Is sufficient waste material for recirculation available and accessible – and what kind of waste material is it?
- Is it possible to ensure demand for both circular products and remaining CO2?
The outlook can be improved by moving further down the value chain and fostering collaboration between multiple industries and across the entire built environment. Creating industrial hubs can help to reduce logistics cost and increase accessibility to waste material. Similarly, the willingness to form networks and collaborate across the built environment will facilitate offtake agreements and enable standardization, such as modular building and design for deconstruction, that increases the potential for circularity.
In the long term, possibilities could arise by shifting from selling concrete not as a material, but in terms of sustainable solutions and services. This approach requires a customer-centric posture to explore new opportunities for green buildings. More specifically, builders and house owners are increasingly requesting sustainable, affordable, durable, and flexible structures, and new ways of thinking how cement and concrete can fulfill these requirements.
What is the World Economic Forum doing about the circular economy?
As customer needs evolve, the entire built environment must follow. Cement and concrete manufacturers that rethink their model – and the built environment value chain more broadly – can secure a stake in opening up new sources of profit.
The authors wish to thank the GCCA for their contribution to this collaborative effort. The World Economic Forum is partnering with GCCA as co-lead of the Mission Possible Partnership’s (MPP) Concrete Action for Climate (CAC) initiative.
Don't miss any update on this topic
Create a free account and access your personalized content collection with our latest publications and analyses.
License and Republishing
World Economic Forum articles may be republished in accordance with the Creative Commons Attribution-NonCommercial-NoDerivatives 4.0 International Public License, and in accordance with our Terms of Use.
The views expressed in this article are those of the author alone and not the World Economic Forum.
Related topics:
The Agenda Weekly
A weekly update of the most important issues driving the global agenda
You can unsubscribe at any time using the link in our emails. For more details, review our privacy policy.
More on Circular EconomySee all
Daniel Boero Vargas and Mandy Chan
April 25, 2024
Margery Ryan and Anis Nassar
April 22, 2024
Johnny Wood
April 18, 2024
Johnny Wood
April 15, 2024
Kiva Allgood and Na Na
March 22, 2024
Valentina Carbone
February 28, 2024