From perfume to hand sanitiser, TVs to face masks: how companies are changing track to fight COVID-19
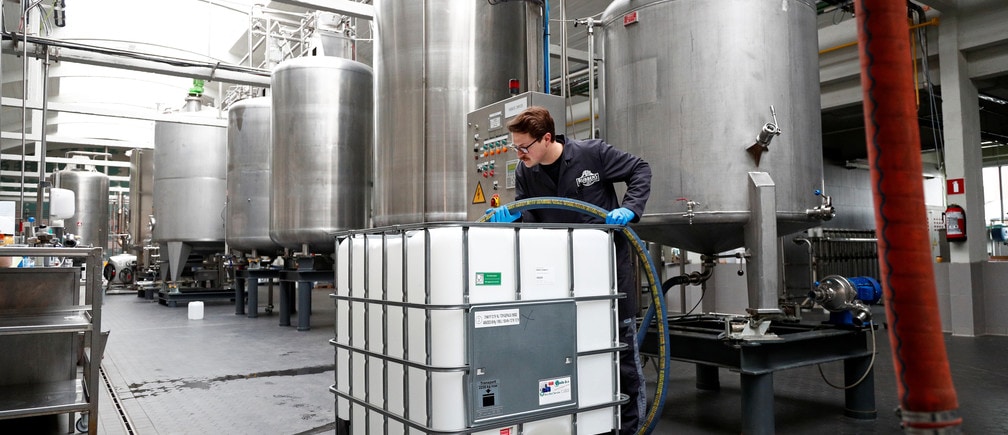
This distillerie is switching from producing gin to disinfecting alcohol during the coronavirus lockdown. Image: REUTERS/Francois Lenoir
Francisco Betti
Head, Global Industries Team; Member of the Executive Committee, World Economic ForumThierry Heinzmann
Project Fellow, Shaping the Future of Advanced Manufacturing and Production, World Economic Forum GenevaExplore and monitor how COVID-19 is affecting economies, industries and global issues
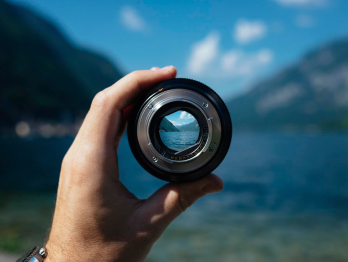
Get involved with our crowdsourced digital platform to deliver impact at scale
Stay up to date:
COVID-19
This article was updated on 13 April 2020.
- Companies are repurposing their production lines to join the fight against COVID-19.
- Examples include LVMH switching from producing perfume to making hand sanitizer, industrial companies making face masks and luxury hotels becoming quarantine centers.
- Companies must overcome different levels of complexity involved as they make these shifts.
The COVID-19 outbreak poses unprecedented challenges to businesses, governments, and societies around the world. Companies are reacting in different ways to ensure business continuity, improve the resilience of their supply chain or pivot to innovative ways to generate revenue.
A key challenge in the current crisis is the demand peak in daily demand for basic consumables such as respirator masks, gowns, visors and swabs. A Kearney analysis estimates a demand surge of about 1’600 percent for masks even in a suppressed disease progression scenario.
One measure that can be observed across industries and countries is companies repurposing their production and R&D capabilities to support the fight against COVID-19. For example, luxury brands like LVMH are switching production lines from producing perfume to making hand sanitizer, industrial companies are making hygienic masks, luxury hotels are becoming quarantine centers, distilleries are creating disinfecting alcohol, and automotive companies are evaluating options to producing urgently needed medical devices such as ventilators.
What is the World Economic Forum doing about the coronavirus outbreak?
Motivation behind repurposing
In times of COVID-19, one of the key priorities for most companies is to protect their own workforce while keeping operations running as long as possible. In many cases (especially for companies in manufacturing) these two objectives require workers to protect themselves - for example, by wearing masks and increasing their use of disinfectants.
In China, the government only allowed companies to re-open manufacturing if, among other measures, enough face masks for employees were available. This led to a surge in demand for such products – demand exceeded supply and companies such as electronic companies Foxconn started to produce face masks themselves with the clear incentive to get production up and running again. These companies quickly build up production capacities for masks and disinfectants that exceeded their own demand, and they started to support frontline medics and others in their daily fight against COVID-19 at no cost.
However, repurposing does not only help companies to protect their own workforce and serving the greater good. Repurposing also helps them to keep production lines up and running in times of low demand, generate moderate revenues, and positively impact their reputation.
Levels of complexity
Several manufacturing companies have started to analyze both the expected capacity projection for their current business as well as the suitability of manufacturing elements to repurpose. In focus is a repurposing of raw materials and components, labour, production process and equipment, as well as the production site and its environment.
Not all sub-segments of an existing manufacturing process are relevant to the product type. For example, motor vehicles and components manufacturing covers a large variety of production facilities. The key is to focus on the sub-segments that are most relevant, such as sound insulation manufacturers that share the same non-woven raw materials and similar production processes with respirator mask manufacturing. Motor vehicle OEMs possessing large and flexible production footprints and deep automation engineering expertise and highly qualified labour should also be considered
One question that always comes up when talking about repurposing is how easy or difficult it is for companies to actually repurpose – especially in manufacturing. To answer this question as it relates to coronavirus, it is crucial to understand that there are different levels of repurposing, with the time required to execute increasing from each one. These are: production of simple hygiene and protection products (e.g., masks and disinfectants); production of standard medical devices (e.g., standard ventilators); and production of more advanced medical devices (e.g., complex ventilators).
Building up capacity and capabilities to produce simple hygiene and protection products such as masks and disinfectants is comparable easy and can be achieved quickly. We have seen companies transforming - for example, research and development sites into dust-free plants - as well as installing related equipment, completing required R&D, and obtaining a certificate to be allowed to produce face masks within days.
A key challenge in this context is to quickly find and qualify suppliers. However, in many cases, the existing supplier base can be leveraged to avoid lengthy qualifications and onboarding processes. For example, car maker Shanghai General Motors Wuling (SGMW) was able to receive medical-grade textiles from a supplier that previously provided interior textile for cars. In another example, ZF Friedrichshafen a German automotive supplier, bought a small, faltering face mask company in China, transported the machines to its factories and produced 100,000 masks a day within two weeks.
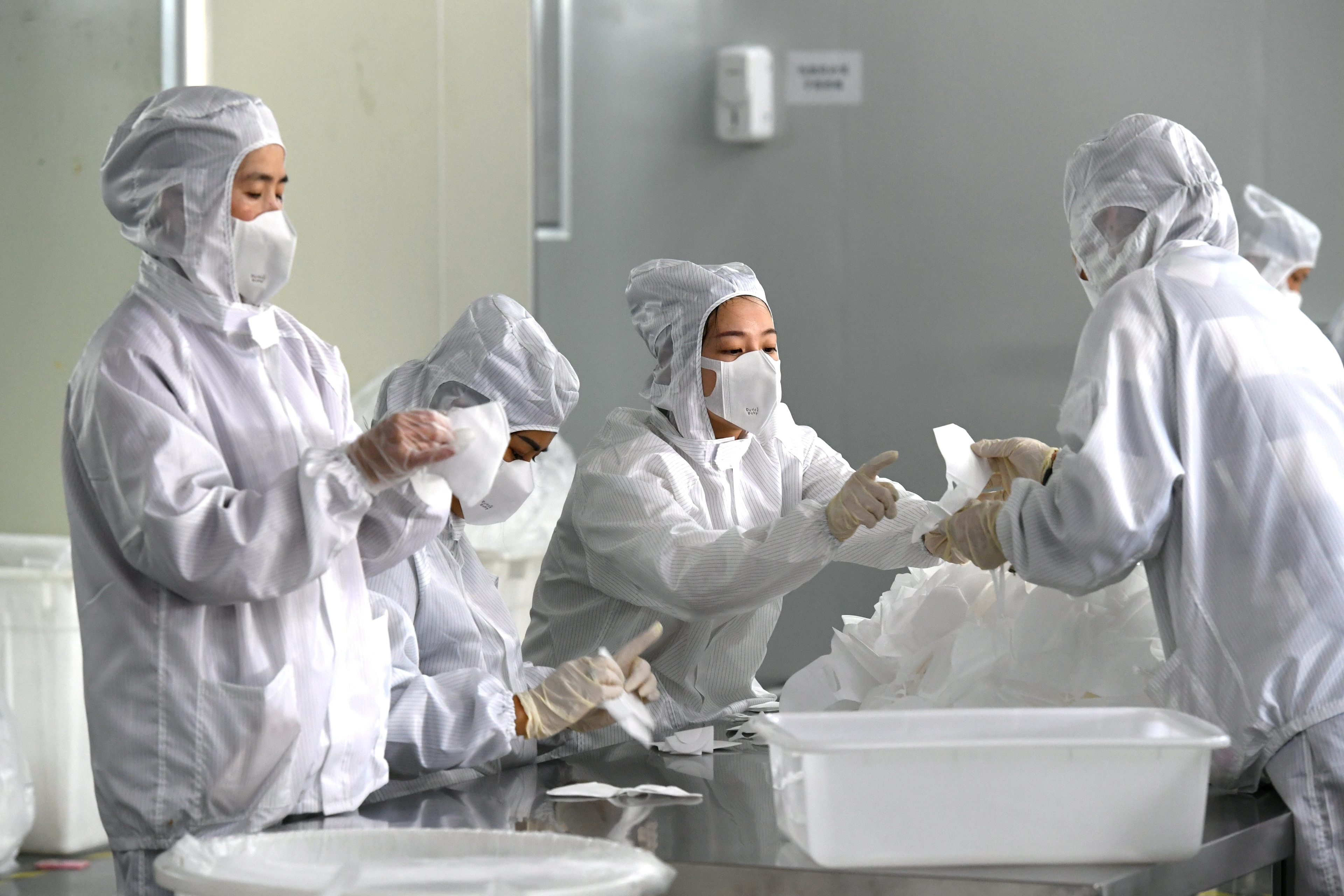
Repurposing manufacturing lines to producing standard medical devices can be complex and takes more time. This option became specifically popular when Elon Musk offered to produce ventilators in his factories if there was a shortage of such products in the nearer future.
While developing the required designs and production process is not too complex for these products, receiving regulatory approval is the key challenge here. Based on different scandals related to the production of medical devices in the past (for example, the breast implement scandal in France that came to light in 2010), authorities have increased regulatory requirements for the production of medical devices through the new European Medical Device Regulation (MDR). Hence, regulatory authorities in Europe and the US will play a key role to make this happen.
The third and most complicated level of repurposing is for non-med-tech companies to start producing things like complex ventilators. The idea here is to use automotive companies' idle capacity to serve as contract manufacturers (CMOs) for medical device companies, which are already producing at their maximum capacity. This level of repurposing would require the sharing of intellectual property on various levels. Hence, it would require collaboration between companies and regulatory authorities.
For example, Dräger, one of the leading manufacturers of sophisticated ventilators, is sceptical about the plans to use idle capacity of German automotive original equipment manufacturers (OEMs). The company focuses on increasing production by switching to three production shifts and the scaling or speeding up of production and quality testing capabilities. The main concern with using other companies as contract manufacturers is that there are large differences in the manufacturing process. Additionally, not just the capacity of the final stage of the manufacturing process would need to increase but also that of suppliers producing the specialized components.
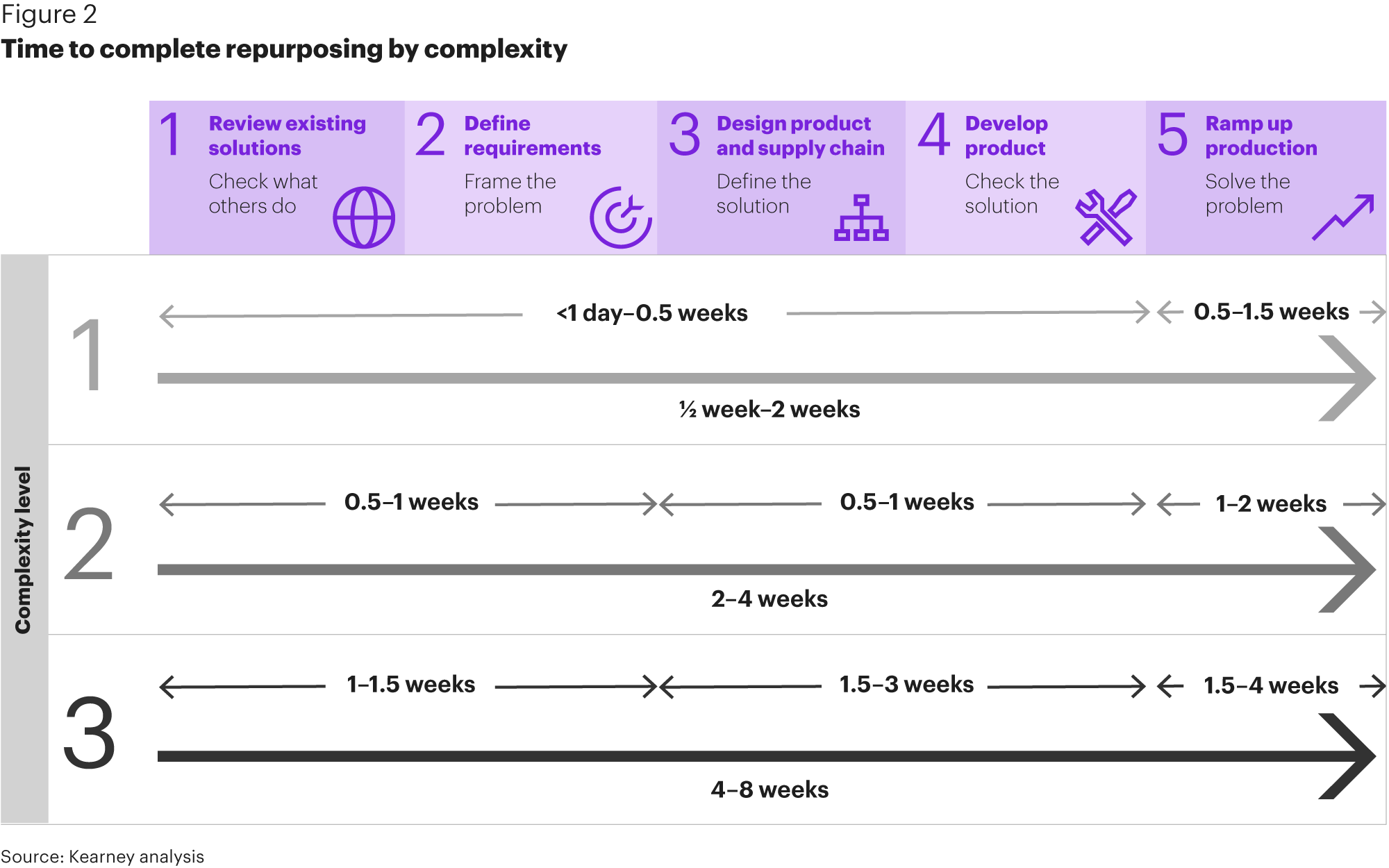
How to repurpose quickly
In a coronavirus-related medical supply shortage situation, activities that normally take months must now be executed in weeks or even days. The only way to achieve this is to sacrifice efficiency for effectiveness.
This requires a simple, five-step approach: review existing solutions, define requirements, design product and supply chain, develop product, and ramp up production. The steps do not need to be followed sequentially but the trade-off of not following the sequence carries a heightened risk of both re-work and unintended consequences. Risk management activities, cross-functional expertise, and single decision-making authority are crucial.
The magnitude of the coronavirus crisis and the scale of resource coordination required has necessitated national- or regional-level governments orchestrating the response. For this reason, a cross-organization, cross-functional government-led task force, or integrated project team, is crucial to concentrate efforts, focus decision-making, and retain flexibility. Key skills needed are from the medical field, product design, prototyping and industrialization, regulations, certification and testing, manufacturing and supply chain, and finance.
Getting the people and process right will ensure a swift and effective response to capacity repurposing. Both should be dedicated to a set problem and should encourage clear reporting lines and immediate communication pathways. The people, organized in an integrated product team, need to include members from all relevant organizations, both internal and external, and should be empowered to take decisions and incentivized to share knowledge with minimal iteration.
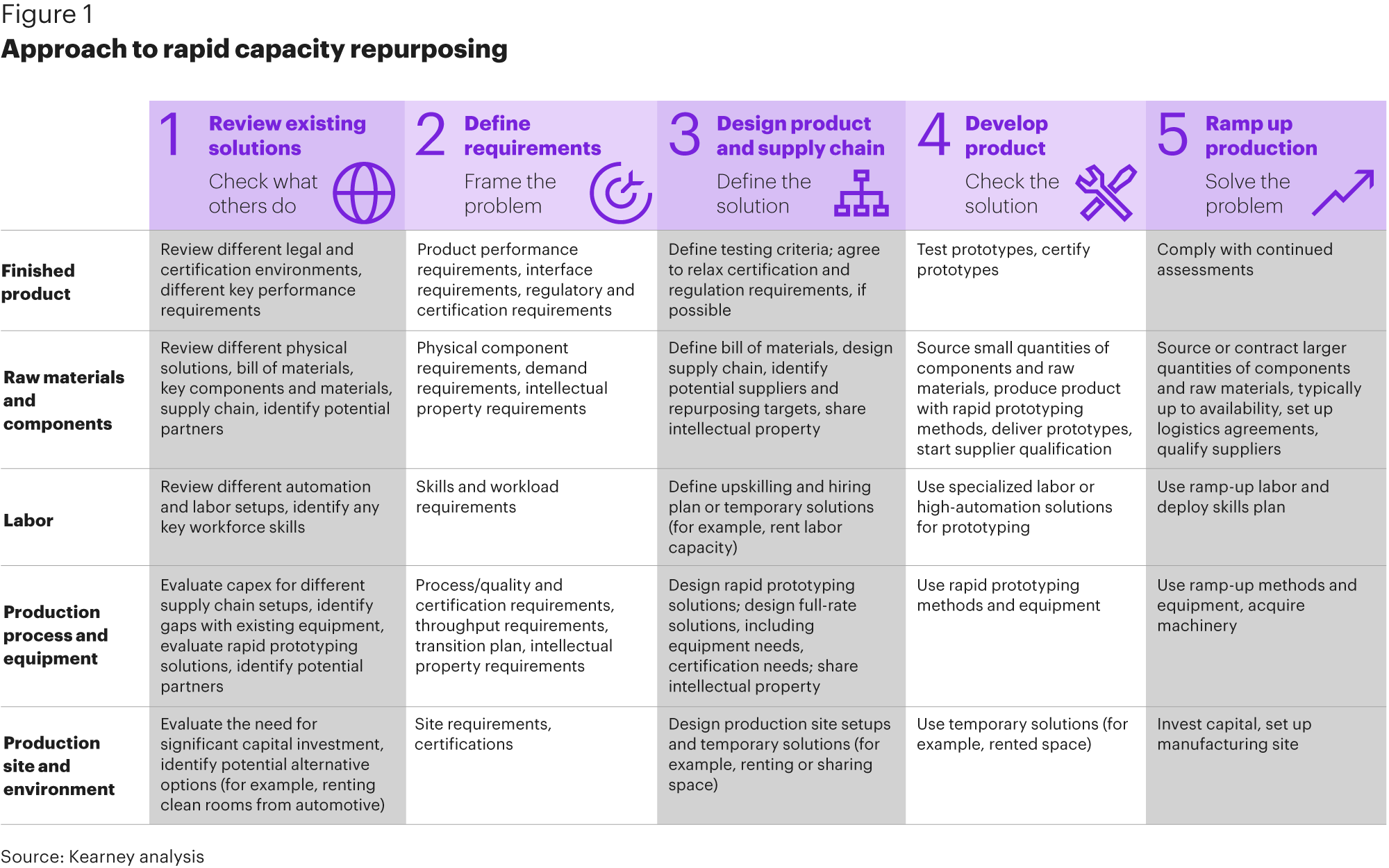
Repurposing beyond manufacturing
There is potential for all industries that are currently facing tremendous demand disruption and connected idle resources to repurpose and develop innovative solutions. One example in this context is the hospitality industry, which already started to pivot from providing accommodation to tourists toward providing space for quarantine centres.
In another industry, retailers started to shift personnel away from physical stores towards supporting digital customer service channels. In Germany, McDonald’s employees are supporting retailer Aldi to cope with the customer rush.
The potential for repurposing beyond manufacturing is tremendous if we think about all the hard-hit areas at the moment, including airlines and restaurants. Extraordinary times call for extraordinary measures.
Per Hong, Senior Partner Strategic Operations at Kearney, Nigel Pekenc, Principal Strategic Operations at Kearney, and Falk Weber, Associate at Kearney, contributed to this article.
Don't miss any update on this topic
Create a free account and access your personalized content collection with our latest publications and analyses.
License and Republishing
World Economic Forum articles may be republished in accordance with the Creative Commons Attribution-NonCommercial-NoDerivatives 4.0 International Public License, and in accordance with our Terms of Use.
The views expressed in this article are those of the author alone and not the World Economic Forum.
Related topics:
The Agenda Weekly
A weekly update of the most important issues driving the global agenda
You can unsubscribe at any time using the link in our emails. For more details, review our privacy policy.
More on Health and Healthcare SystemsSee all
Katherine Klemperer and Anthony McDonnell
April 25, 2024
Vincenzo Ventricelli
April 25, 2024
Shyam Bishen
April 24, 2024
Shyam Bishen and Annika Green
April 22, 2024
Johnny Wood
April 17, 2024