Digital spare parts: Manufacturing's solution to supply chain woes
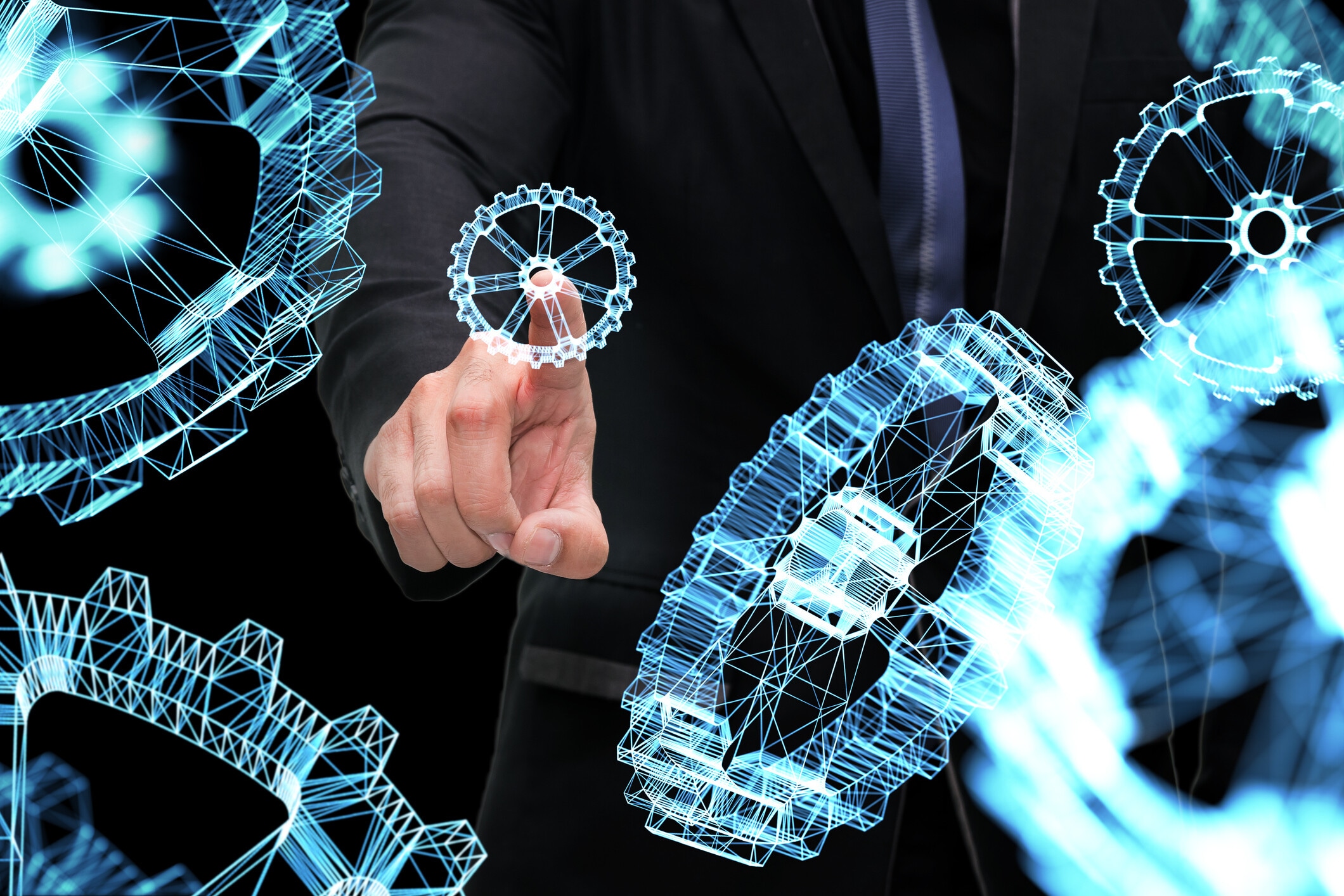
Digital spare parts offer a solution to the manufacturing industry's woes of supply chain disruption and warehousing costs. Image: Getty Images/iStockphoto
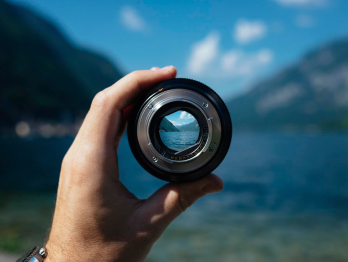
Get involved with our crowdsourced digital platform to deliver impact at scale
Stay up to date:
Advanced Manufacturing and Supply Chains
- As the global manufacturing industry has changed, access to critical spare parts or sectors like energy and defense has become more challenging.
- Coupled with supply chain disruptions and growing warehousing costs, addressing the spare part issue is becoming business critical.
- Digital spare parts, made using advanced manufacturing techniques, could offer a solution.
In the years following the Second World War, many of the world’s most developed nations were flush with industry. Post-war reconstruction meant rebuilding cities, critical infrastructure and disrupted sectors. The golden age of manufacturing, which stretched into the early 1970s, brought many nations and industries new-found wealth built on a foundation of iron and steel.
Over time, however, manufacturing slowed, plants closed and jobs moved overseas. However, the equipment used to operate critical industries like energy, defense and transportation (among others) remained. Though built to perform in harsh conditions, these assets are aging, and the need to sustain them with spare parts is becoming more pressing.
Fifty years after the global recession of the 1970s, we have yet to address the spare parts problem definitively. For the energy industry, that spells trouble.
Manufacturing's spare parts problem
The spare parts problem is the lack of necessary parts to sustain obsolete equipment. This equipment, either no longer manufactured by suppliers or long-since modernized, still fulfills a critical need to maintain operations for essential industries like energy — and the lack of these parts comes at a considerable price.
By some measures, production equipment failures cost industrial manufacturers an estimated $50 billion annually. A 2022 report by Siemens revealed that for the Oil and Gas (O&G) sector, “the cost of an hour’s downtime has more than doubled in just two years, to almost $500,000.” The report further indicates that the annual downtime cost for each O&G facility is $149 million per year, “despite businesses in this sector cutting the number of failures by 25% and the total amount of downtime by 16%.”
Though planned and predictive maintenance lessen the blow that downtime causes, it’s not the only solution. For industries like energy, whose availability can impact economic outcomes and quality of life, the consequences of downtime can be severe. In 2023, the US Centers for Disease Control and Prevention (CDC) published a report revealing that of the 470 fatalities that occured between 2014 and 2019 at oil and gas extraction sites — and, in 13.4% of those fatalities, workers were carrying out repair or maintenance.
Knowing that downtime is both costly and dangerous, technology that can reduce operational downtime through greater part availability offers a compelling argument. This is where digital spare parts come into play.
Digital spare parts: A solution for manufacturing
Digital spare parts are a method in which spare parts manufacturing data is stored and transferred digitally. These spare parts “digital twins” can be produced point-of-need using additive manufacturing (AM) technologies, or with other rapidly deployable advanced manufacturing methods like rapid casting and CNC milling.
In particular, using AM technologies can address two severe disadvantages of spare part procurement via traditional supply chains. First, digital spare parts produced by AM can shorten production lead times. Whether by producing qualified end-use parts or expediting injection molding with 3D-printed casts, on-demand production can save months, if not years, of procurement lead time.
The second disadvantage of traditional supply chains, addressed by digital spare parts, is the cost of warehousing. In 2018, global companies were spending upwards of $320 billion per year on warehousing — a figure that has undoubtedly surged in recent years due to post-COVID-19 supply chain disruptions. Digital spare parts, on the other hand, empower organizations to develop their digital inventories of ready-to-print parts to offset stock-keeping costs and free up capital otherwise locked in slow-moving replacement parts.
How manufacturing can integrate digital spare parts
So, digital spare parts are the answer, but how do organizations transition from traditional spares into a digital-first approach?
Perhaps the answer for the energy industry’s spare parts problem lies with the defense industry, which has some of the world’s most complex logistics and supply chains. Mission criticality means that spare parts must be immediately available, (much like energy), and that means investing in technologies and processes that modernize equipment sustainment.
There are two approaches to answering the digital spare parts conundrum: digitize everything or digitize only the most promising parts.
To demonstrate the former, Wichita State University’s National Institute for Aviation Research (NIAR) has successfully created digital twins for critical US Department of Defense assets like the M113 armored personnel carrier, B1-Bomber and the Black Hawk helicopter. Equipped with these digitized parts, branches of the military can evaluate them for additive manufacturing to determine whether parts can be 3D printed and, if so, with what materials. They can also assess digital parts to determine the total cost of manufacturing using advanced manufacturing methods like additive versus traditional supply chains.
The second approach is to evaluate parts before digitizing them to create a priority list of parts that can be fast-tracked for qualification as digital spares. The United States Marine Corps. Advanced Manufacturing Systems Team (USMC AMST) worked with 3YOURMIND to do just that. In the programme's first year, 10,000 parts were analyzed based on part drawings, 3D files and data points to make evaluations that suggested which parts make the best technical and business use cases for additive manufacturing. These findings support the USMC’s efforts to develop its Digital Manufacturing Data Vault, which essentially functions as a centralized repository to store information, including digital spare parts, in anticipation of on-demand manufacturing.
The spare parts problem will not go away unless we break away from frail, high-margin, just-in-time manufacturing supply chains and instead pivot to a digital-first approach. This investment in modern manufacturing doesn’t just support the sustainment of aging assets in operation today; it also prepares us to address the next generation of equipment sustainment challenges.
By adopting digital solutions and investing in tomorrow’s manufacturing techniques, we can ensure the continued operation of existing assets while positioning ourselves to tackle future challenges with agility and efficiency. It’s time to embrace the transformative power of technology to secure the reliability and longevity of our equipment and make ourselves more resilient to future supply chain disruptions.
Don't miss any update on this topic
Create a free account and access your personalized content collection with our latest publications and analyses.
License and Republishing
World Economic Forum articles may be republished in accordance with the Creative Commons Attribution-NonCommercial-NoDerivatives 4.0 International Public License, and in accordance with our Terms of Use.
The views expressed in this article are those of the author alone and not the World Economic Forum.
The Agenda Weekly
A weekly update of the most important issues driving the global agenda
You can unsubscribe at any time using the link in our emails. For more details, review our privacy policy.
More on Manufacturing and Value ChainsSee all
Andre S. Yoon and Kyoung Yeon Kim
April 23, 2024
Andrea Willige
March 19, 2024