Why advanced manufacturing must always nurture skilled people
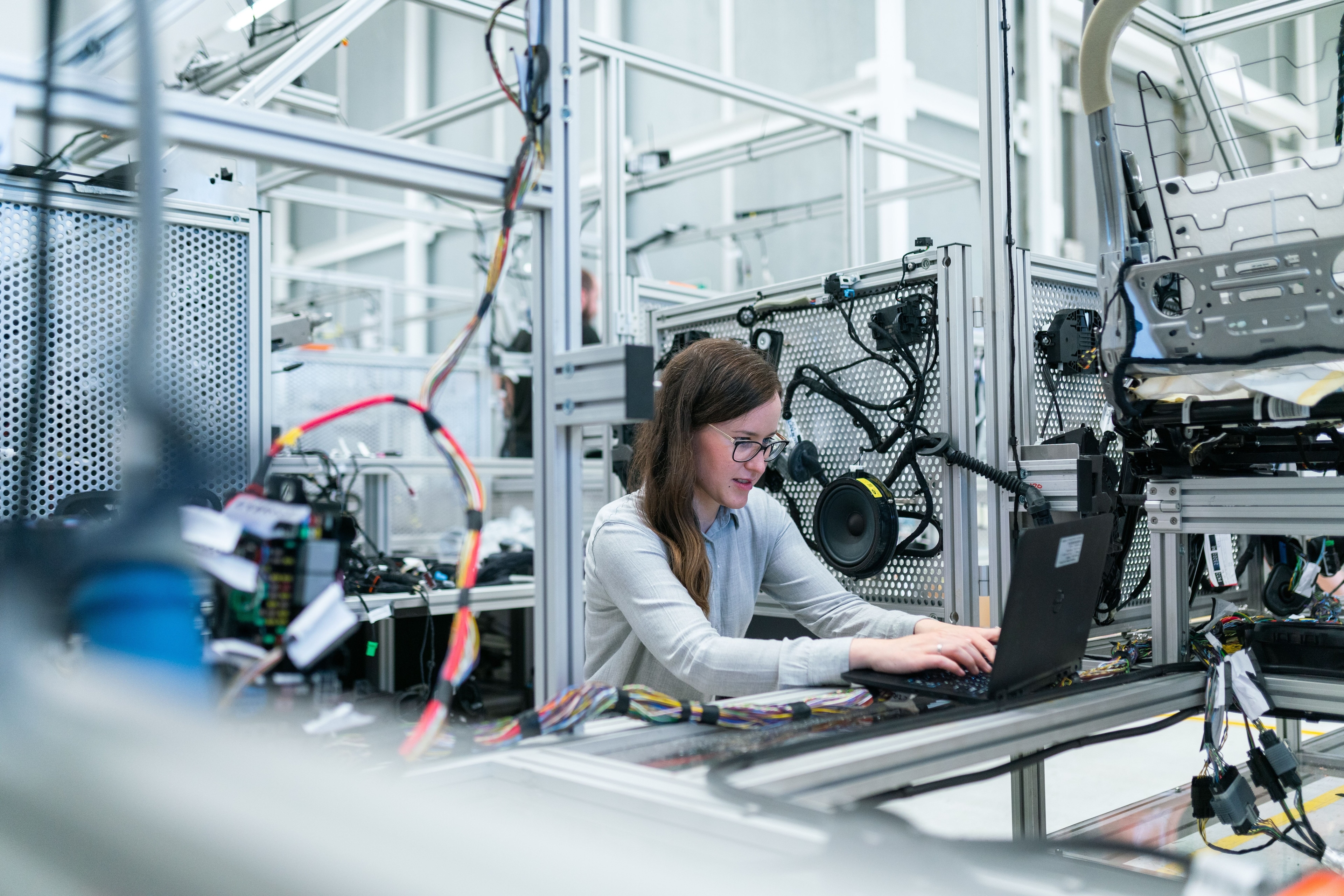
The World Economic Forum’s New Narrative for Advanced Manufacturing emphasizes the human element of manufacturing’s future. Image: Photo by ThisisEngineering RAEng on Unsplash
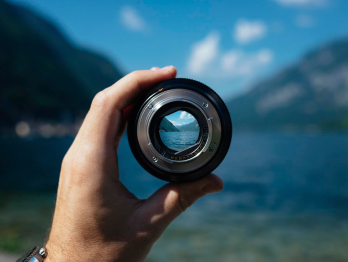
Get involved with our crowdsourced digital platform to deliver impact at scale
Stay up to date:
Advanced Manufacturing
- Skilled individuals remain the backbone of the manufacturing industry worldwide.
- The World Economic Forum’s New Narrative for Advanced Manufacturing emphasizes the human element of manufacturing’s future.
- We must invest in our workforce — and their safety, wellbeing and career fulfilment — if we are to harness the full potential of Industry 4.0.
Across the globe, the manufacturing sector is experiencing a seismic shift driven by geopolitics, supply-chain disruptions, climate change and tech innovation. Consequently, a new strategic emphasis on the workforce is crucial. This must recognize that skilled individuals are the backbone of the industry – the power behind resilience, innovation and sustained productivity in this rapidly evolving landscape. A recent survey conducted by the National Association of Manufacturers (NAM) found that “almost three-quarters of surveyed manufacturing executives feel that attracting and retaining a quality workforce is their primary business challenge.” With this level of focus on building the talent pipeline, it’s clear that Industry 4.0 isn’t just the future of manufacturing; it’s the future of the world’s workforce.
Introduced in September 2023, the World Economic Forum’s New Narrative for Advanced Manufacturing provides a roadmap for how advanced manufacturing solutions can unlock new value for industries and organizations around the world. Although the five impact areas of the New Narrative are closely interlinked, zeroing in on the human element of manufacturing’s future is crucial.
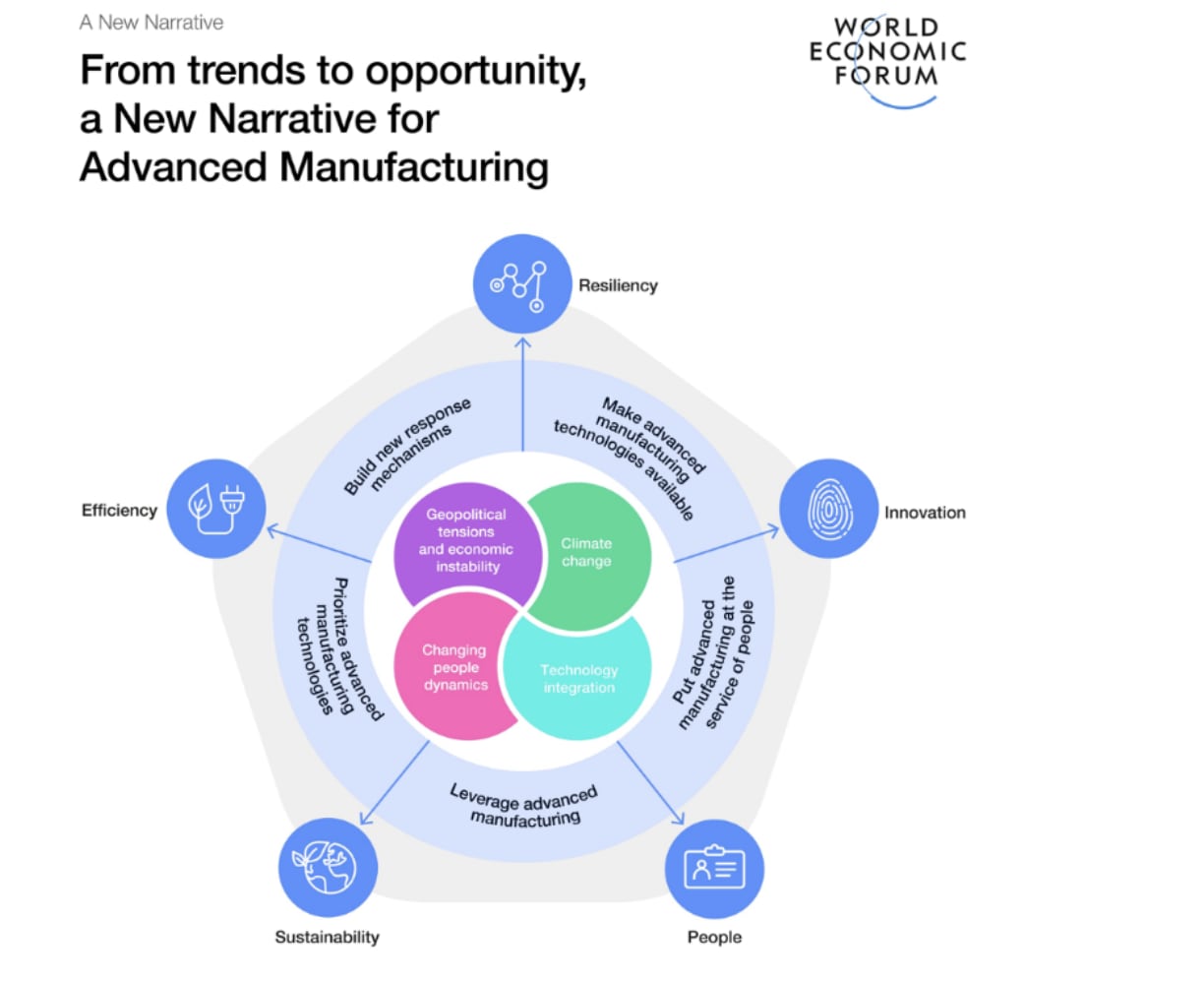
As the CEO of Flex, a global diversified manufacturer, I resonate the most with the New Narrative impact area described as People: Empowering workers and society for a just transition. Flex has a global workforce of approximately 170,000 people in 30 countries. As a leader, one of my greatest responsibilities is to ensure that our commitment to doing the right thing, always, is embedded in the organization. It’s also crucial to create a work environment that is safe and inclusive and that enables people to do their best work.
I began my career as a shop-floor supervisor in Shawnee, Oklahoma. I recognize firsthand the value that workers on the factory floor bring to our industry. When I travel to Flex’s many sites around the world, I always make a point to walk the factory floor and to meet the people who are at the heart of making great products for our customers.
The importance of recognizing the unique contributors of the workforce to the developing manufacturing process is a view echoed by Maya Ben Dror, Industry Manager of the Automotive and New Mobility & Advanced Manufacturing at the World Economic Forum and co-author of the New Narrative report. She says: "Within the evolving landscape of geopolitics and technological advancements, I enjoy curating advanced manufacturing leadership as an affirmation that skilled hands and creative minds breathe life into progress. In the software-driven era, the enduring spirit of manufacturing thrives when we prioritize the nurturing of a skilled workforce — vital for positive global impact.”
The imperative of accessibility, inclusivity and safety
The implementation of advanced manufacturing technologies makes the factories of the future safer, more accessible and more inclusive for all workers. With the right technology, we can improve worker wellbeing and safety, while making jobs available to a broader range of applicants when certain requirements — such as the ‘ability to lift’ or visual acuity — are removed.
Robotics and automation can remove human workers from repetitive and potentially dangerous settings, while reducing other risks commonly found on the factory floor — from injuries due to lifting heavy items to accidents caused by distracted or disengaged workers. This aligns with the New Narrative’s assertion that advanced manufacturing technologies can be used to “expand the range of tasks and jobs available to new employees, promoting flexibility, productivity and equity and facilitating the integration of individuals with disabilities in shop-floor activities.”
An October 2023 white paper released by the National Safety Council on implementing technologies to reduce most common workplace musculoskeletal disorders (MSDs) stated that “as workplaces undergo a transformation… the intricate interactions between workers and their workplaces can be simplified by automating work processes or integrating emerging technologies to eliminate or minimize worker exposure to ergonomic hazards.”
As companies implement new technologies, they must also examine how they can make the workplace safer for all. Cross-sector collaborations in the World Economic Forum’s initiatives underscore the concrete advantages of prioritizing accessibility, inclusivity and safety in advanced manufacturing. Elevating workplace safety not only safeguards the well-being of workers, but also enhances productivity and job satisfaction. Leveraging advanced technologies to eliminate physical barriers and redefine job requirements fosters diversity and inclusivity, expanding the talent pool.
Ultimately, new technologies deliver real, concrete benefits to the people who form the heart of the manufacturing industry. The economic benefits of using technologies to improve worker experience include greater efficiency, innovation and competitiveness in the global market. As the manufacturing landscape evolves, investments in accessibility and inclusivity contribute to a safer, more diverse workforce, translating into long-term business success.
The Flex CEO perspective on how people are the most important element in manufacturing.
Fostering a culture of education and lifelong learning
To advance Industry 4.0, we should also offer education and training opportunities to provide workers — both those already working in the manufacturing industry and those interested in joining — with the technical skills needed to thrive in the factories of the future. This work requires deep collaboration between governments, nonprofits, academic institutions and corporations so that as a society, we stand behind our investment in the people at the centre of manufacturing.
At Flex, we have implemented multiple programmes around the world to provide training opportunities and fulfilling career pathways. This includes:
• Our Capability Acceleration Programme, which has trained over 9,000 (and counting) global employees on a broad range of disciplines and skills, including automation, extended reality and more.
• At our site in Suzhou, China, we partnered with local government in 2019 to provide ongoing education to our direct labour force and have since trained over 500 employees.
• We launched a learning centre in Jalisco, Mexico, to train more than 2,000 employees annually on topics including mount tech, robotics assembly and more.
Collaboration across public and private spheres is key to achieving the greatest impact. To that end, Flex has relationships with educational institutions around the world. We partner with Midlands Technical College in Columbia, South Carolina, to provide entry-level manufacturing skills. And, in Malaysia, we partnered with Jabatan Pembangunan Kemahiran, a government agency, to develop the National Dual Training System. These are just a few examples of how we can provide lifelong learning opportunities to people in manufacturing so they can grow their skills and remain motivated and engaged.
Coming together to put people first
People have always been at the heart of the manufacturing industry, so it follows that we must invest in the technologies and practices that empower our workforce — and their safety, wellbeing and career fulfilment — if we are to harness the full potential of Industry 4.0.
Our Advanced Manufacturing Industry community continues to demonstrate how we can come together to offer solutions to global disruptions and a path to more innovative, inclusive and sustainable industry transformation. Together, we can usher in a new era of manufacturing, while improving the lives of people everywhere. It is only when we embrace our interconnectedness in advancing the future of manufacturing that we can realize the full potential of human ingenuity and innovation.
Don't miss any update on this topic
Create a free account and access your personalized content collection with our latest publications and analyses.
License and Republishing
World Economic Forum articles may be republished in accordance with the Creative Commons Attribution-NonCommercial-NoDerivatives 4.0 International Public License, and in accordance with our Terms of Use.
The views expressed in this article are those of the author alone and not the World Economic Forum.
The Agenda Weekly
A weekly update of the most important issues driving the global agenda
You can unsubscribe at any time using the link in our emails. For more details, review our privacy policy.
More on Manufacturing and Value ChainsSee all
Aleksander Ciszek and Devin Culham
April 25, 2024
Andre S. Yoon and Kyoung Yeon Kim
April 23, 2024
Andrea Willige
March 19, 2024