How to find and fix hidden factories
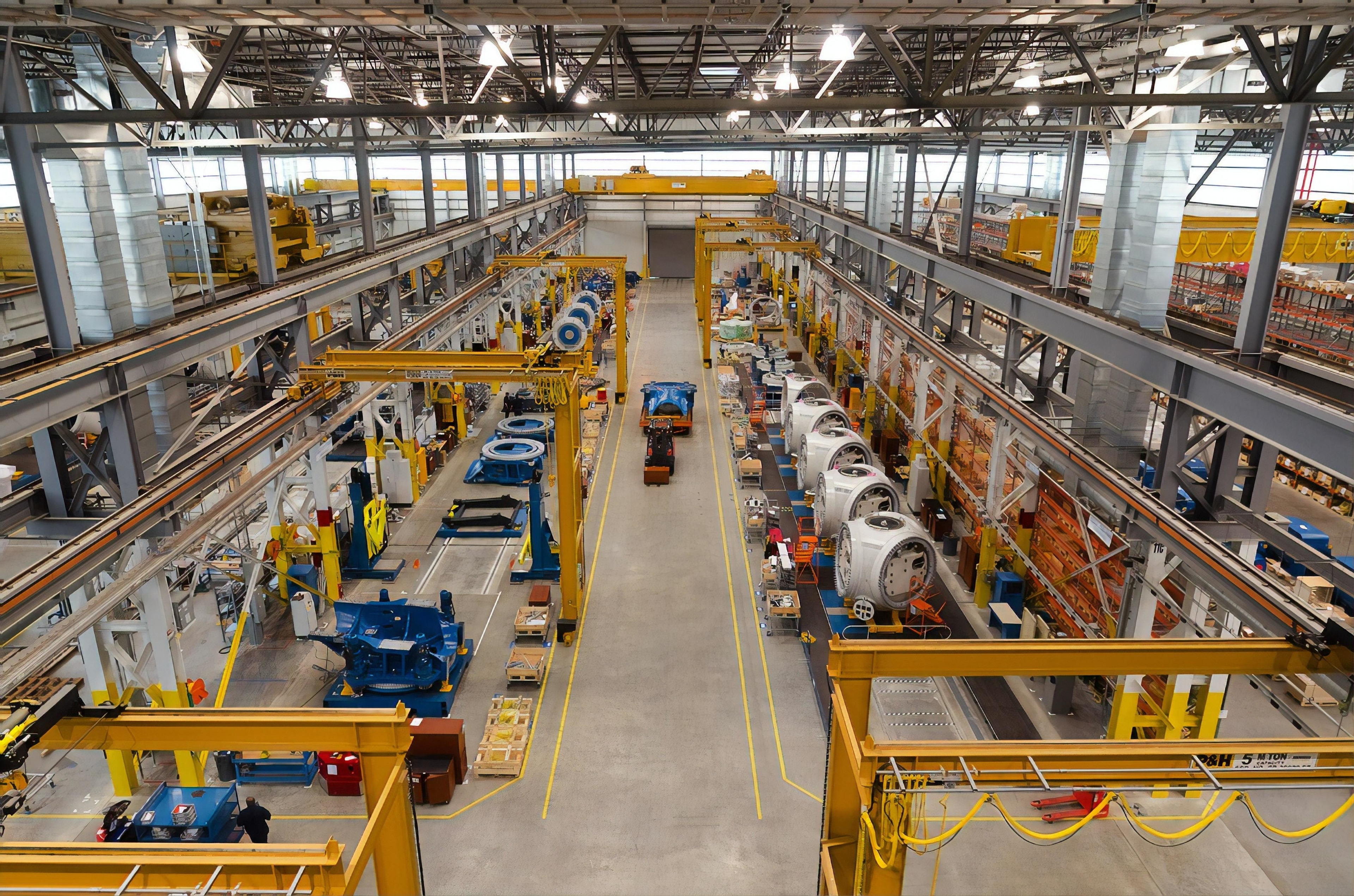
What workarounds are happening at your work?
Image: Unsplash/Science in HD
Stay up to date:
Education, Gender and Work
- The term 'hidden factory' explains what happens when processes go wrong and people devise workarounds that become institutionalized.
- The divergence from expectation and reality can reduce productivity, profitability and sustainability of an organization.
- So, how can you identify and tackle these hidden factories?
As a leader, do you ever feel that there is lost capacity within your current system, but can’t quite figure out how to find and release it? Do you feel the constant request for more resources will only make it worse?
Armand Feigenbaum, author of “Total Quality Control,” found himself in a similar situation at a General Electric Co. facility in the early 1960s.
“Thirty percent of the activities he observed in the factory were unplanned, unscheduled, and didn’t serve the customer,” saidJohn Carrier,a senior lecturer at MIT Sloan and an expert in systems dynamics. “It was just people running around, random chaos.”
Feigenbaum, an MIT Sloan alumnus, alighted on the term “hidden factory” to describe what he saw. In essence, when processes go wrong, people devise workarounds on the fly. Over time, these myriad workarounds become institutionalized; processes as they were designed increasingly diverge from what happens in practice. This dramatically reduces the productivity, profitability, and sustainability of an organization.
Feigenbaum’s insight, it turns out, applies not only to traditional operations, but to manufacturing and product development across the world. Nearly any type of work process in any industry can be scrambled by hidden factories. Carrier, who works with companies to identify and deconstruct hidden factories, spoke with MIT Sloan to summarize best practices when approaching the problem.
Accept our marketing cookies to access this content.
These cookies are currently disabled in your browser.
Finding what’s hidden
As the name suggests, hidden factories are difficult to see. They result from an accumulation of many small extemporaneous changes. A culture builds around them, with its own language: absorption costing, allowances, refactoring, reprioritization, etc. It then creeps into the architecture of the operations itself — as the enterprise resource planning systems are customized to accommodate the hidden factories, rather than used to eliminate them.
“My first step is usually to meet with the schedulers, and ask ‘Are we planners and schedulers, or re-planners and re-schedulers?’ In the ‘as planned’ facility, you plan, schedule, and execute. In the ‘as is’ facility, hidden factories insert themselves into the plan, leading to constant rescheduling.
The trick to finding hidden factories is, in one sense, easy: look for missing time, Carrier said. Assess, for example, the timeliness of customer delivery. (Most firms Carrier has worked with run around 60-70% of orders on time prior to his intervention.) After that, look at which tasks get rescheduled and reprioritized and in what ways. Third, study maintenance logs; if deferrals are a constant issue and there is a large and growing backlog of maintenance, then somewhere a hidden factory is slowing systems down.
Carrier noted two other symptoms to look for when trying to find hidden factories. First, find parts of a system that are under pressure, particularly time pressure. This hunt can be as simple as asking employees what causes the most stress in their job. Second, find places in the system where products and processes are stalled while waiting to move to the next stage. Long queues suggest a hidden factory.
Addressing the problem
In the 1990s, furniture manufacturer Herman Miller was feeling squeezed to move factories overseas. Leadership, though, was loath to abandon the Michigan communities in which the company had been rooted for almost a century. The company searched for, found, and addressed inefficiencies; manufacturing remains in Michigan.
The core of this work was not a round of layoffs or a massive push for leaner production. Rather, the company engaged with an effort to “reduce human struggle,” Carrier said. This slogan — more readily affiliated with political revolution than corporate cost-savings — is what informed the hunt for hidden factories.
“That’s how you find the friction within your operations,” Carrier said. “You change the way you measure things.”A few specific approaches to fixing hidden factories include:
Make space for the little things. Companies like to throw their efforts behind solving big problems. This can be problematic when it comes to hidden factories, as, despite their costliness, they comprise dozens or hundreds of small inefficiencies. Carrier calls this the 10,000 pennies problem. “You won’t find dollar bills lying on the factory floor,” he said. “But hidden factories are 10,000 pennies sitting around.”
Engage as many employees as possible. From the top of the company, Carrier suggests that CFOs need to be involved in this work. Only they can provide necessary investment and properly measure outcomes. But strong leadership is not enough. Because hidden factories tend to be dispersed across many parts of a system, crafting an effective solution requires engagement with a large swath of a company. Carrier suggests that no less than 30% of employees should be recruited to work toward solutions.
Importantly, when searching for hidden factories employees should focus on how time, not cost, is spent. “If you constantly chase cost reduction, you will ultimately wear the system down into total failure,” Carrier said.
Focus on risk, not productivity. There is a conventional view of risk and productivity as tightly coupled: greater productivity implies greater risk, and vice versa. “This is based on the assumption that the system is operating at its ‘efficient frontier,’ which is rarely the case,” Carrier said. If you tackle risk in the right way — addressing the parts of a system that are overtaxed — then you can reduce the risk while increasing productivity. Hidden factories left untended, meanwhile, are both unproductive and unsafe.
Invest in the system, not new technology. Technology can, of course, help to shrink hidden factories, but at its root this problem is about culture and information, not technology. Before anything else, knots in the system must be worked out, and the informational gaps that led to those knots repaired. New technologies or algorithms can’t help if the system and the culture it has nurtured remain broken.
Look for duct tape, clamps … and spreadsheets. The hidden factory has its own set of tools – of the “get-'er-done” variety. In operations, it consists of duct tape, C-clamps, crescent wrenches, and the ratchet extension that someone bent using a blowtorch. In the office, the major culprit is the spreadsheet, where work that falls outside the workflow application — be it Jira or an SAP or Salesforce application — is funneled into the hidden factory of office work. This hidden work is then protected from detection by PowerPoint waterfall diagrams, meticulously prepared to smooth out any disturbing information that would be useful for addressing the factors behind the formation of the hidden factory, Carrier said.
Encourage open communication. Workarounds and quick fixes are unavoidable. Building a system free of defects, Carrier said, would be prohibitively expensive, if not impossible. The key is to have rapid and routine feedback when workarounds occur, and to then respond accordingly. To this end, open and honest communication is essential. “If you have a culture where employees are expected to report only good news to senior leadership, then they’ll just filter out information that they think they shouldn’t share,” he said. “To paraphrase W. Edwards Deming, ‘You’ve just created the perfect system to institutionalize hidden factories.’”
Seek hidden factories in software development and knowledge work. In the software world, the hidden factory phenomenon is revealed in terms such as anti-patterns and technical debt. Unsurprisingly, the development and operations world is adopting the same concepts and tools to address them: Kanban, fast delivery cycles, and value stream mapping. “There are far more hidden factories in software and back-office processing than in any physical manufacturing,” Carrier said.
In the end, Carrier explained that the search for hidden factories should be viewed, above all else, as an opportunity. “Hidden factories are actually good things because they are the system’s way of telling you where to focus,” he said. “This is a gift. You want them to go away, but know also that the system is speaking to you.”
Don't miss any update on this topic
Create a free account and access your personalized content collection with our latest publications and analyses.
License and Republishing
World Economic Forum articles may be republished in accordance with the Creative Commons Attribution-NonCommercial-NoDerivatives 4.0 International Public License, and in accordance with our Terms of Use.
The views expressed in this article are those of the author alone and not the World Economic Forum.
Related topics:
Forum Stories newsletter
Bringing you weekly curated insights and analysis on the global issues that matter.
More on LeadershipSee all
Antara Choudhury and Vivin Rajasekharan Nair
August 14, 2025
Jan Oliver Schwarz and Katharina Kleine
August 12, 2025
Ida Jeng Christensen and Raju Narisetti
August 5, 2025
Martin Adams
July 30, 2025
Anil Gupta and Wang Haiyan
July 25, 2025