Bone implants to be made from 3D printed salt
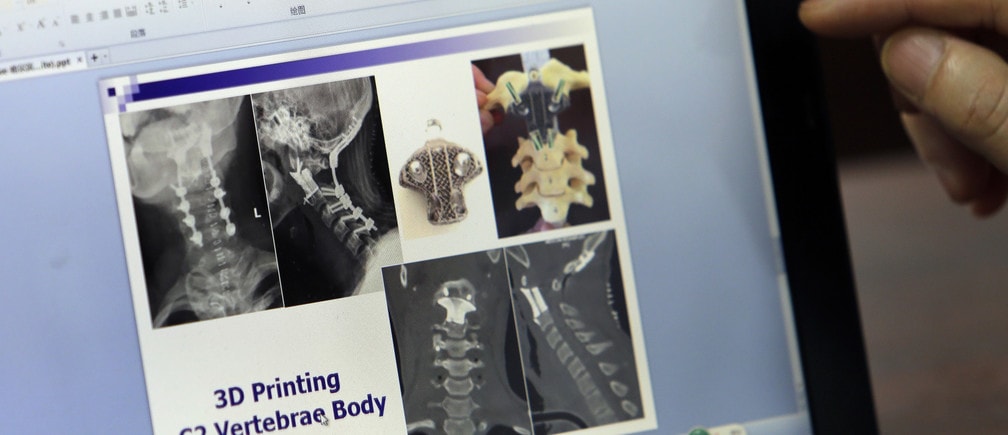
To promote rapid healing, the design of implants or their surfaces need to promote cellular adhesion or even growth into the implant
Image: REUTERS/Jason Lee (CHINA - Tags: SCIENCE TECHNOLOGY HEALTH) - GM1EA8M0C3R01
Stay up to date:
3D Printing
For the treatment of complex bone fractures or even missing bone parts, surgeons typically deploy metal implants. In this context, biodegradable magnesium and its alloys are attractive alternatives to the traditional materials like bioinert titanium. Implants made of the light metal are advantageous because they can biodegrade in the body, which can absorb magnesium as a mineral nutrient, rendering a second surgery for implant removal unnecessary.
To promote rapid healing, the design of implants or their surfaces need to promote cellular adhesion or even growth into the implant. Researchers have therefore developed a new procedure for the manufacture of magnesium implants that contain numerous structurally ordered pores but still retain their mechanical stability.
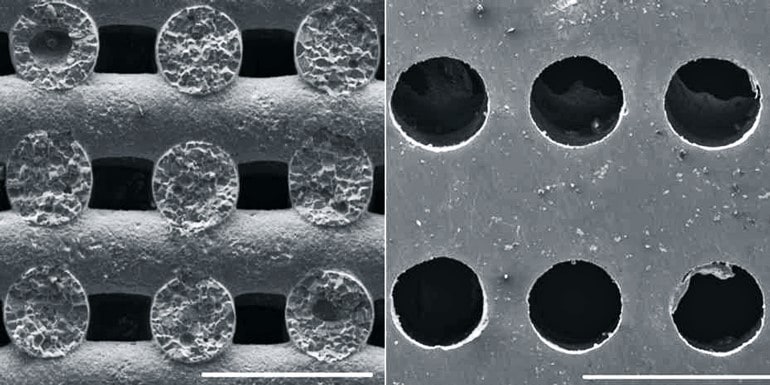
To create a porous structure the researchers first printed a three-dimensional salt template using a 3D printer. Because pure, standard table salt is not suitable for printing, they developed a gel-like salt paste for this purpose. The researchers can use the printing process to tailor the strut diameters and spacings of the salt template.
To gain sufficient mechanical strength, the researchers subsequently sintered the salt structure. During sintering, researchers heat the fine-grained materials significantly, while choosing a temperature that’s safely below the paste’s melting point to retain the structure of the workpiece.
The next step was to infiltrate the pores with magnesium melt. “The infiltrates obtained in this way are mechanically very stable and can be easily polished, turned, and shaped,” says Jörg Löffler, professor of metal physics and technology in the materials department at ETH Zurich. After mechanical shaping the researchers dissolved the salt, leaving a pure magnesium implant with numerous, regularly structured pores.
“The possibility to control the pore size, distribution, and orientation in the material is decisive for clinical success, because bone cells like to grow into these pores,” says Löffler. This process is key for the rapid integration of the implant in bone.
The new procedure for manufacturing these template structures from salt can also be applied to other materials besides magnesium. The researchers expect that the process could help tailor pore geometries in polymers, ceramics, and other light metals.
The idea of this new manufacturing procedure came out of the Master’s thesis of Nicole Kleger, now a doctoral student in the Complex Materials Group of André Studart, under whose direction researchers 3D printed the initial salt template. An ETH Zurich Excellence Scholarship & Opportunity stipend supported Kleger’s initial study. In her doctoral thesis project, Kleger is now developing the 3D-printing procedure further.
The research appears in Advanced Materials.
Don't miss any update on this topic
Create a free account and access your personalized content collection with our latest publications and analyses.
License and Republishing
World Economic Forum articles may be republished in accordance with the Creative Commons Attribution-NonCommercial-NoDerivatives 4.0 International Public License, and in accordance with our Terms of Use.
The views expressed in this article are those of the author alone and not the World Economic Forum.
Related topics:
Forum Stories newsletter
Bringing you weekly curated insights and analysis on the global issues that matter.
More on Health and Healthcare SystemsSee all
Gareth Francis
June 12, 2025
Shyam Bishen
June 10, 2025
Carolina Aguilar
June 5, 2025